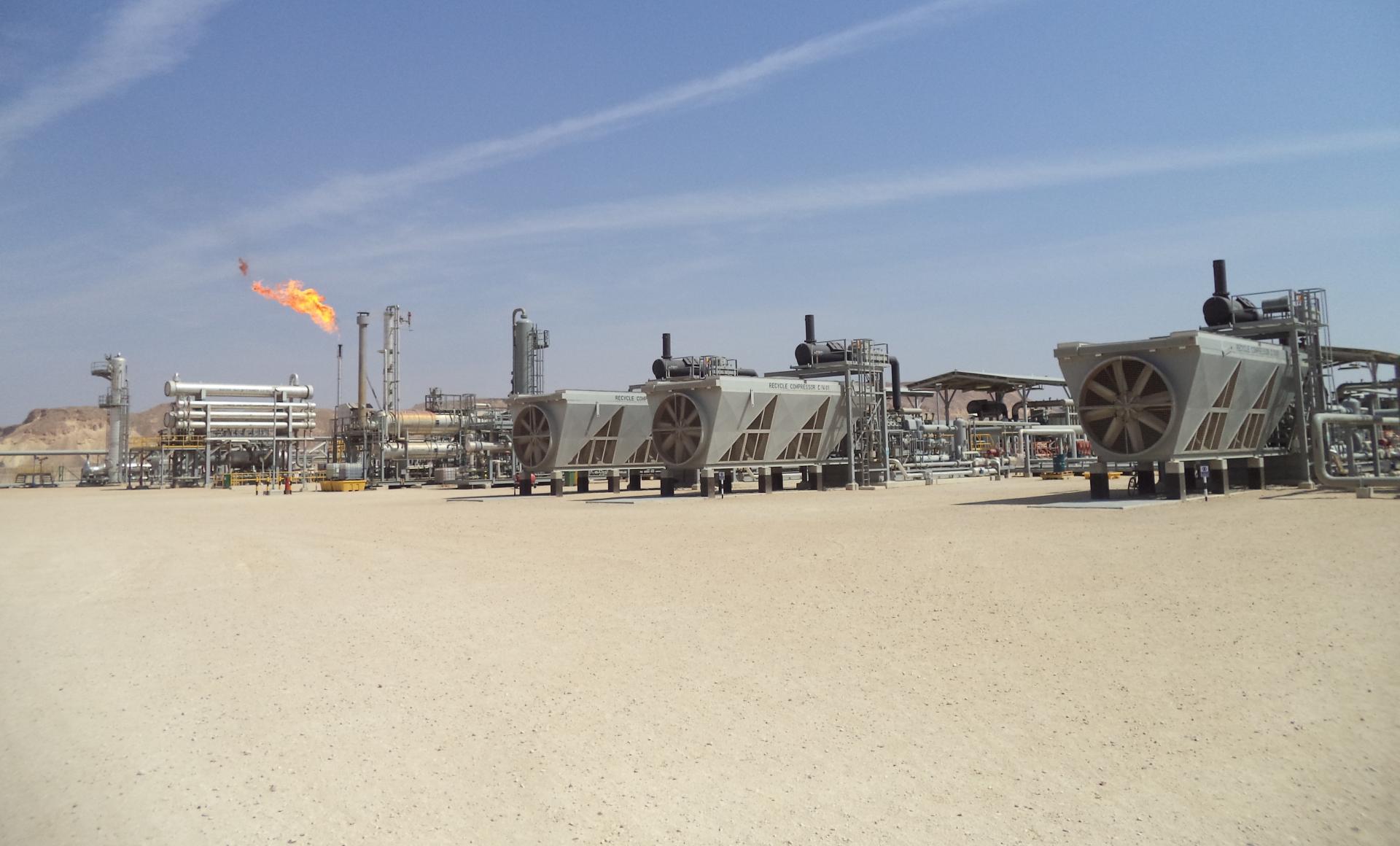
Equipment / Gas Treating
Flare Gas Recovery
Turn Waste Gas Into Revenue
Transform flare gas into valuable energy while reducing emissions and costs. Enerflex’s customized solutions make flare gas recovery an economic and environmental win.
The Enerflex Edge
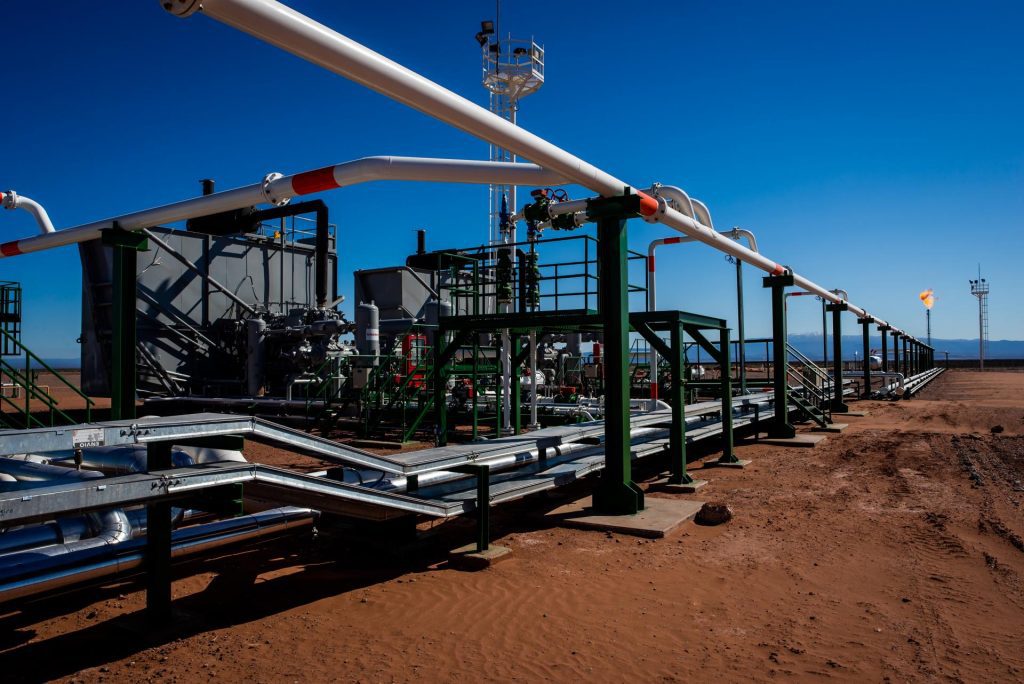
Wide-Ranging Custom Solutions for Every Scale Abilities
We customize Flare Gas Recovery Systems (FGRS) for both large and small applications, with flow rates up to 10 MMSCFD and pressure up to 300 psig.
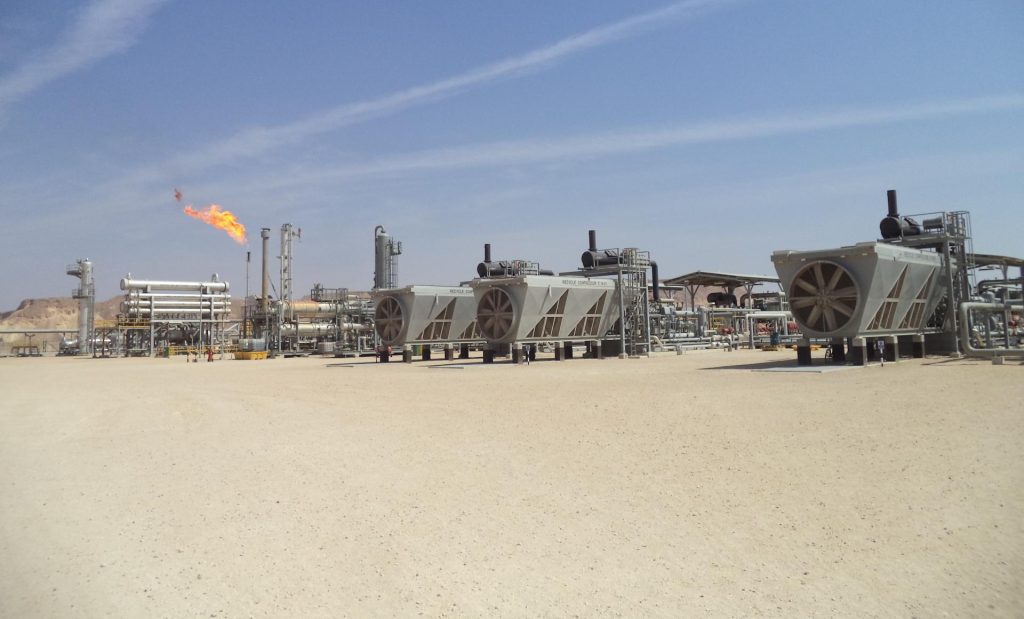
Global Expertise, Local Know-How
With extensive experience across diverse regions, Enerflex brings effective flare gas recovery solutions to markets worldwide.
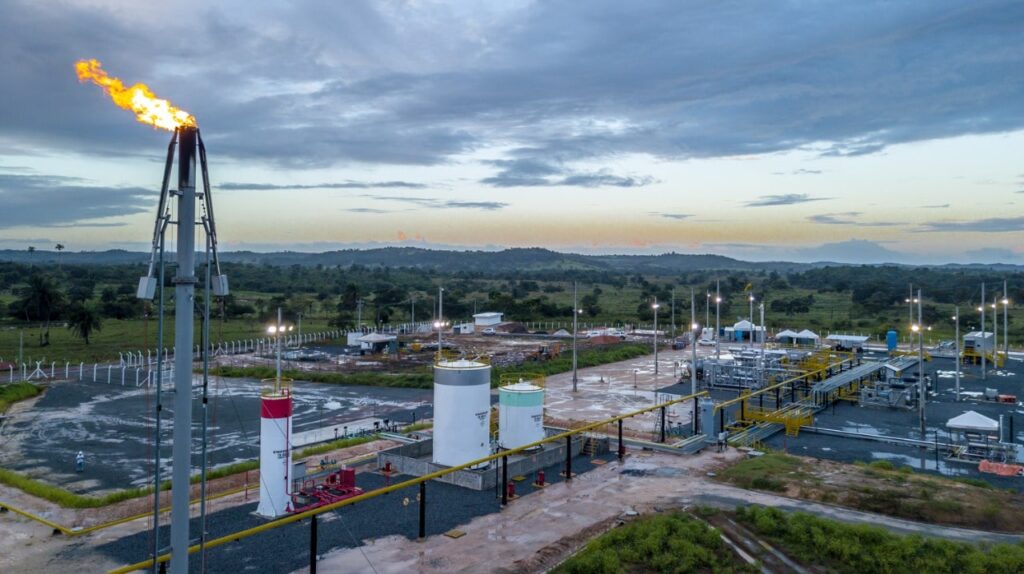
Maximized Cost Savings & Compliance
Our solutions reduce operating expenses by repurposing waste gas so clients can benefit from lower fuel costs and compliance incentives.
Case Study
9.6 MW Power Station with Flare Gas-to-Power Solution
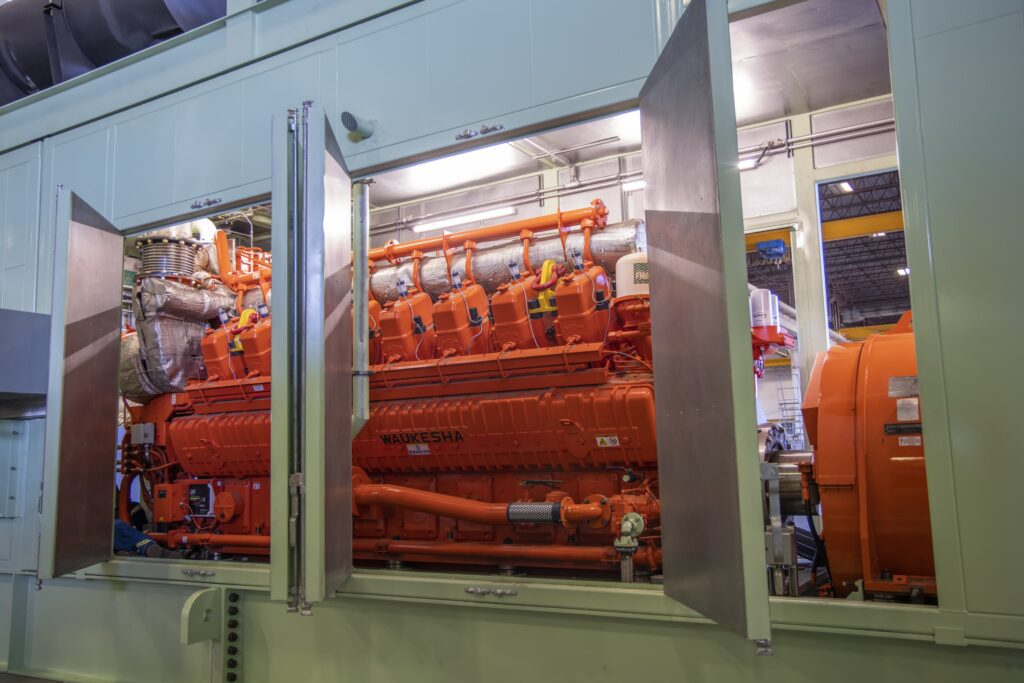
Challenge:
Our client partner needed a reliable power solution for a remote facility in Colombia, completely isolated from any power grid. The site required 9.6 MW of continuous power, with flexibility for future expansion.
Solution:
We supplied a modular power solution with three PWC3200S units, each generating 3,200 kW for a total output of 9.6 MW at 4,160V and 900 RPM. The package featured a 16V 275GL+ Waukesha engine, Kato generator, Sutton Stromart cooler and ComAp Intelisys NTC control system, housed in a custom walk-in enclosure.
Outcome:
Our solution ensured reliable power across a challenging landscape, operating from 1.6 MW to 9.6 MW. Pre-commissioning at our Houston facility enabled adjustments before final installation, leading to commissioning a week ahead of schedule and within budget.
Electric Power
Our power solutions convert flare gas into reliable electricity, providing a dual benefit of emissions reduction and energy production. Scalable systems handle various fuel types, ensuring consistent power—even in remote locations.
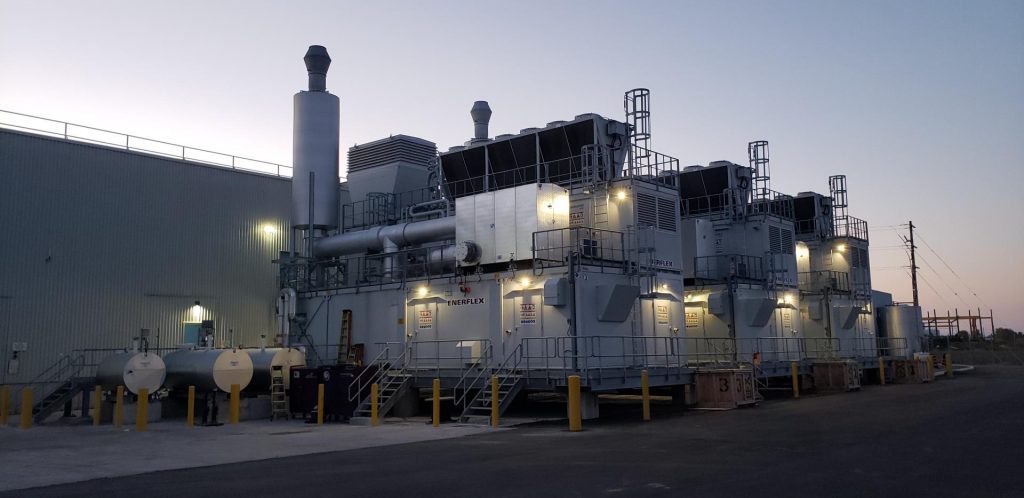
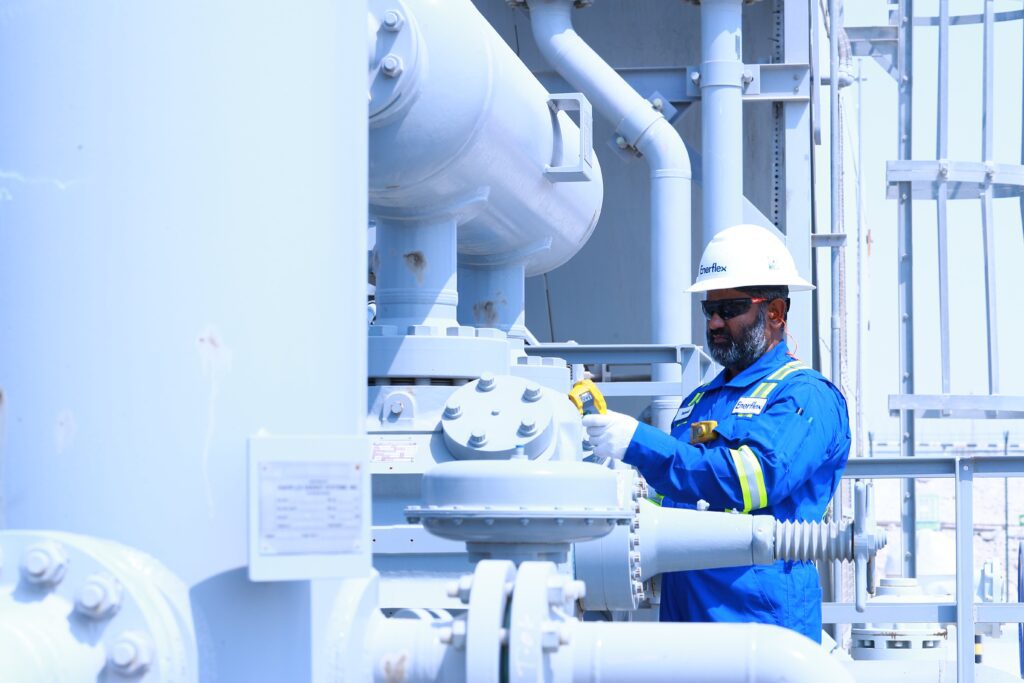
Operations and Maintenance
Our teams provide 24/7 support for Flare Gas Recovery Systems, ensuring safety, reliability and efficiency. Skilled technicians help minimize downtime, maintain compliance and maximize your return on recovered gases.