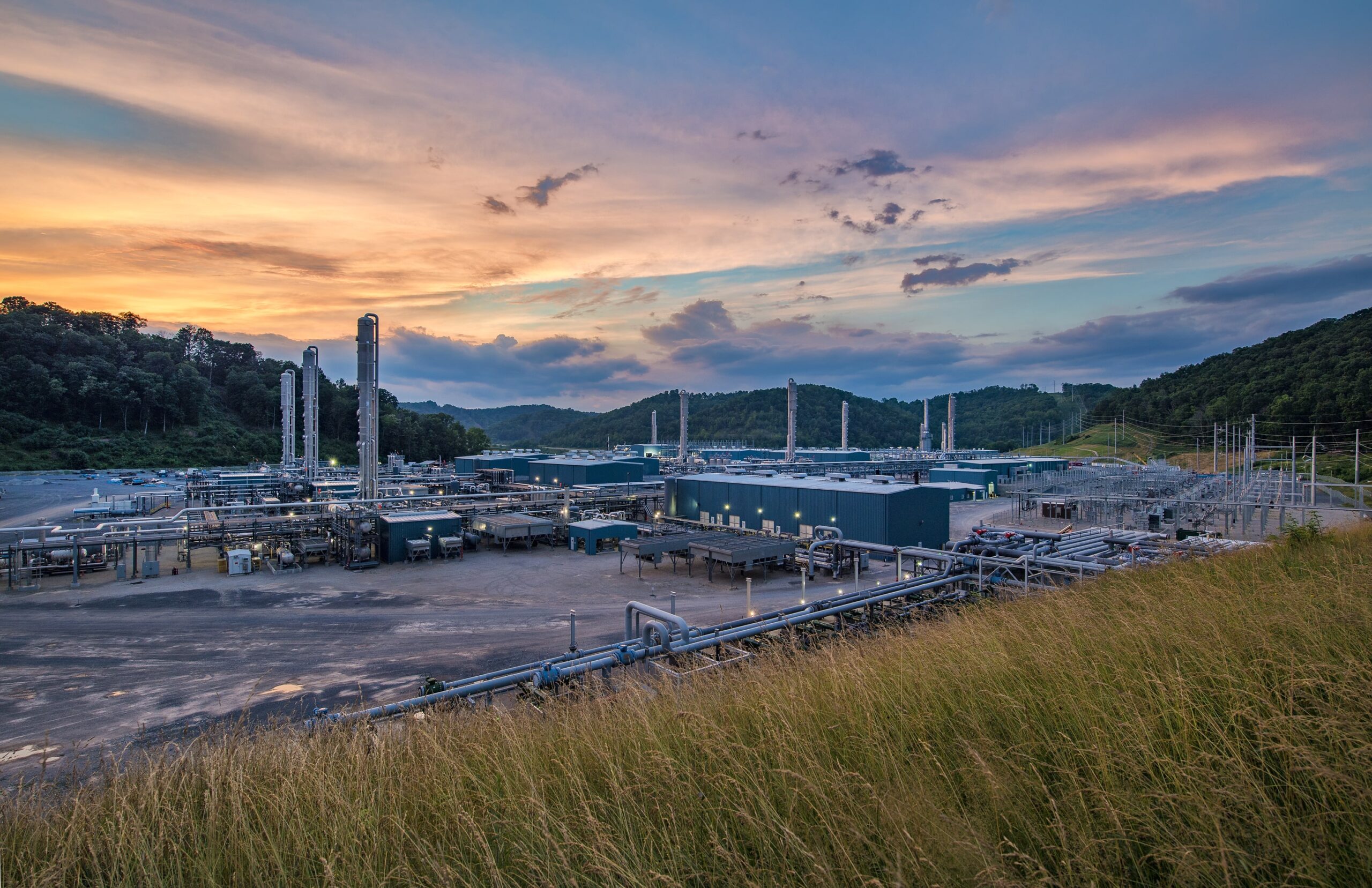
Infrastructure
BOOM
Efficient Project Execution for Faster Gas Monetization
Partnering with Enerflex means accelerating every phase of your project. We deliver integrated solutions through our Build-Own-Operate-Maintain (BOOM) model that brings gas to market faster—maximizing efficiency, reducing costs and driving profitability. Enerflex’s experienced BOOM team manages every aspect of natural gas processing and treating facilities, water treatment facilities, and compression plants, including operations and maintenance.
Comprehensive Solutions Driving Speed to Market and Reducing Risks
Our BOOM model offers a turnkey approach that spans every stage of your project. With fixed costs, our solutions minimize financial uncertainty and mitigate risk. By managing the full scope, we streamline execution and ensure your facility operates efficiently for years to come.
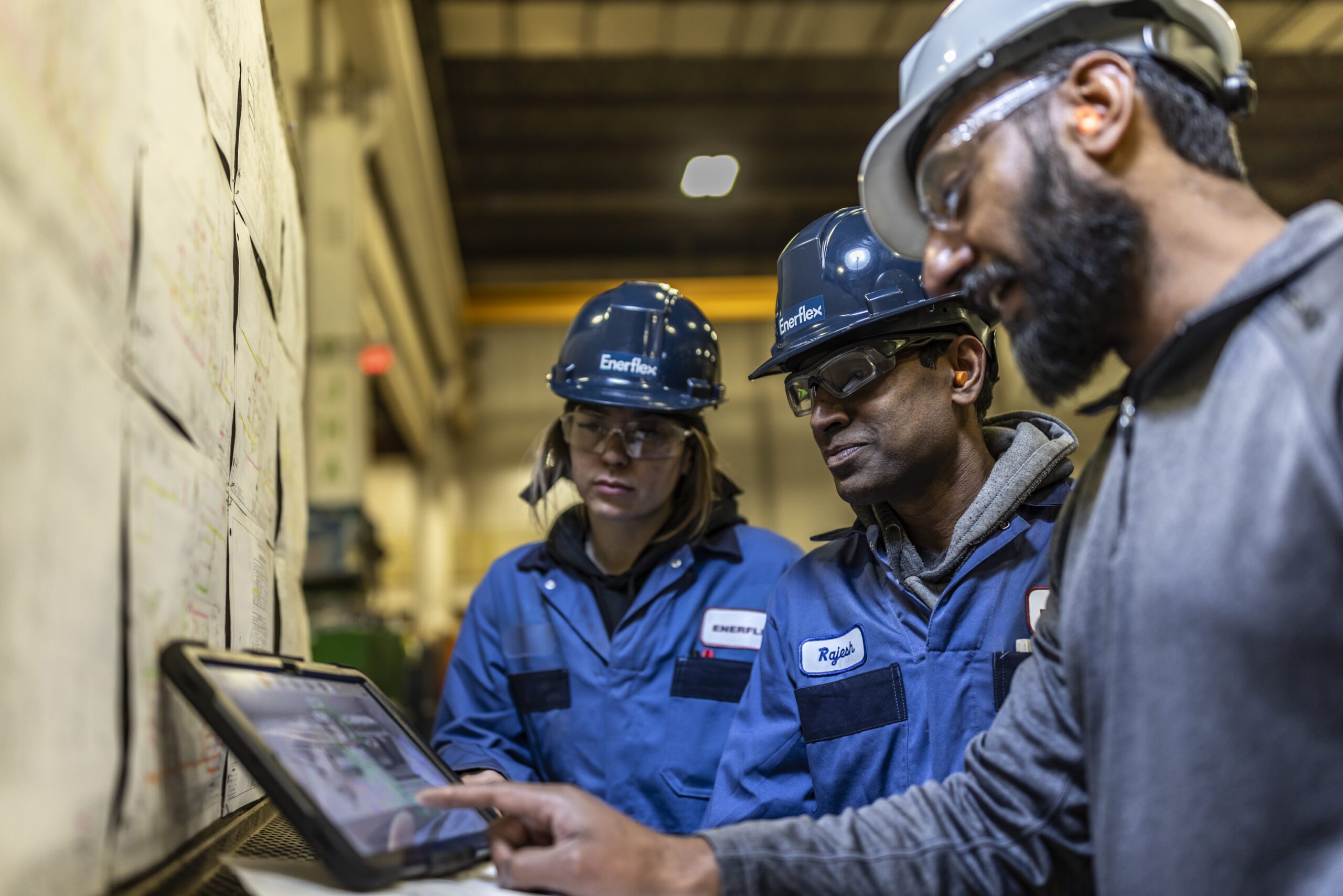
- FEED study design
- Detailed drawings
- High level solutions design
- P&IDs
- Process engineering
- Full cost esimtate and high-level project plan

- Modular / Skid fabrication and assembly
- Latest manufacturing processes and technologies
- Quality control
- Region specific ISO certifications
- In-house trial fit capabilities
- Raw material and component procurement
- Equipment OEM alliances
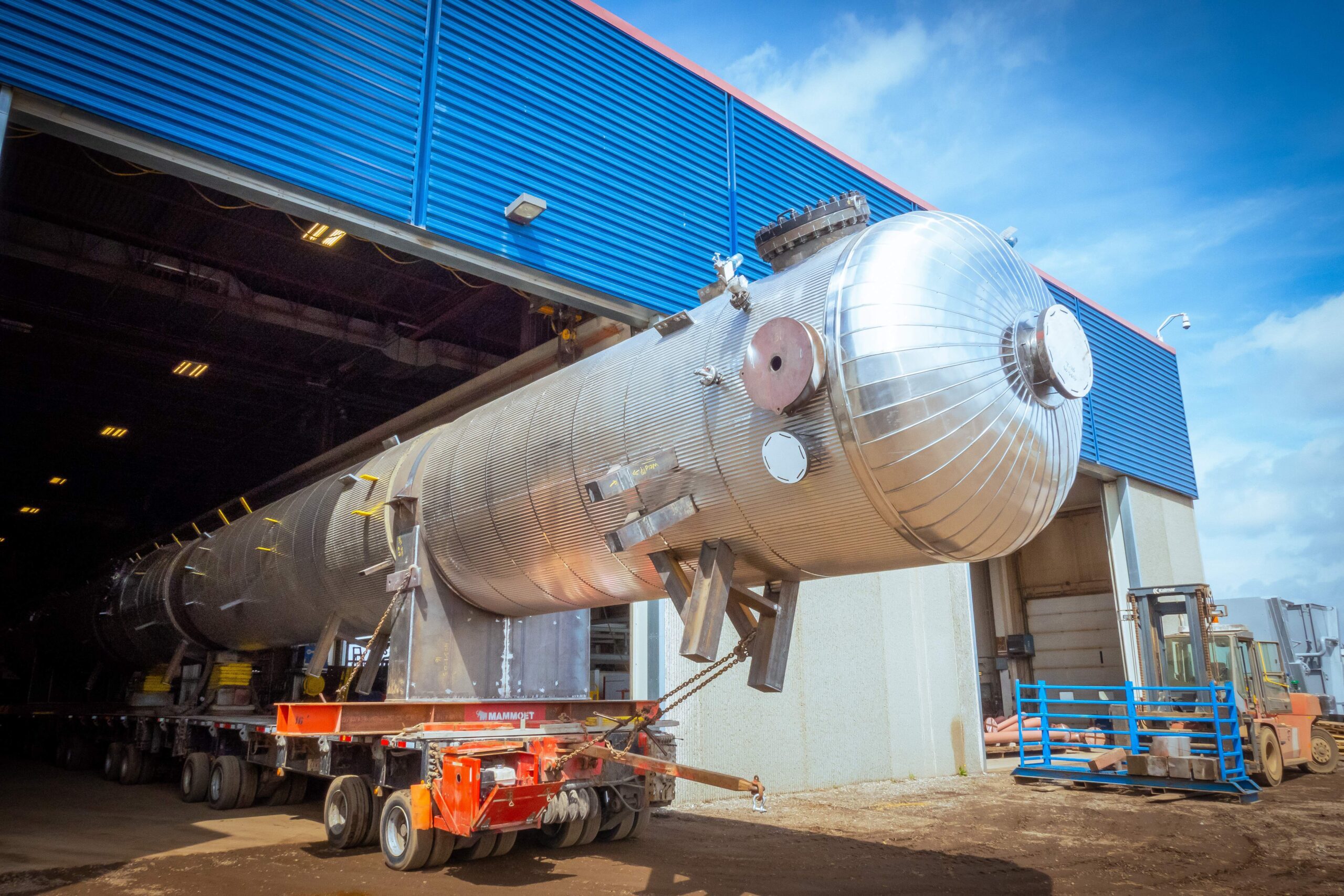
- Integrated network for packing, shipping, and delivery for ease of installation in the field
- Strategic relationships with third-party logistics providers
- Manufacturing facility located near Southern USA tidewater ports and Western Canadian gas fields
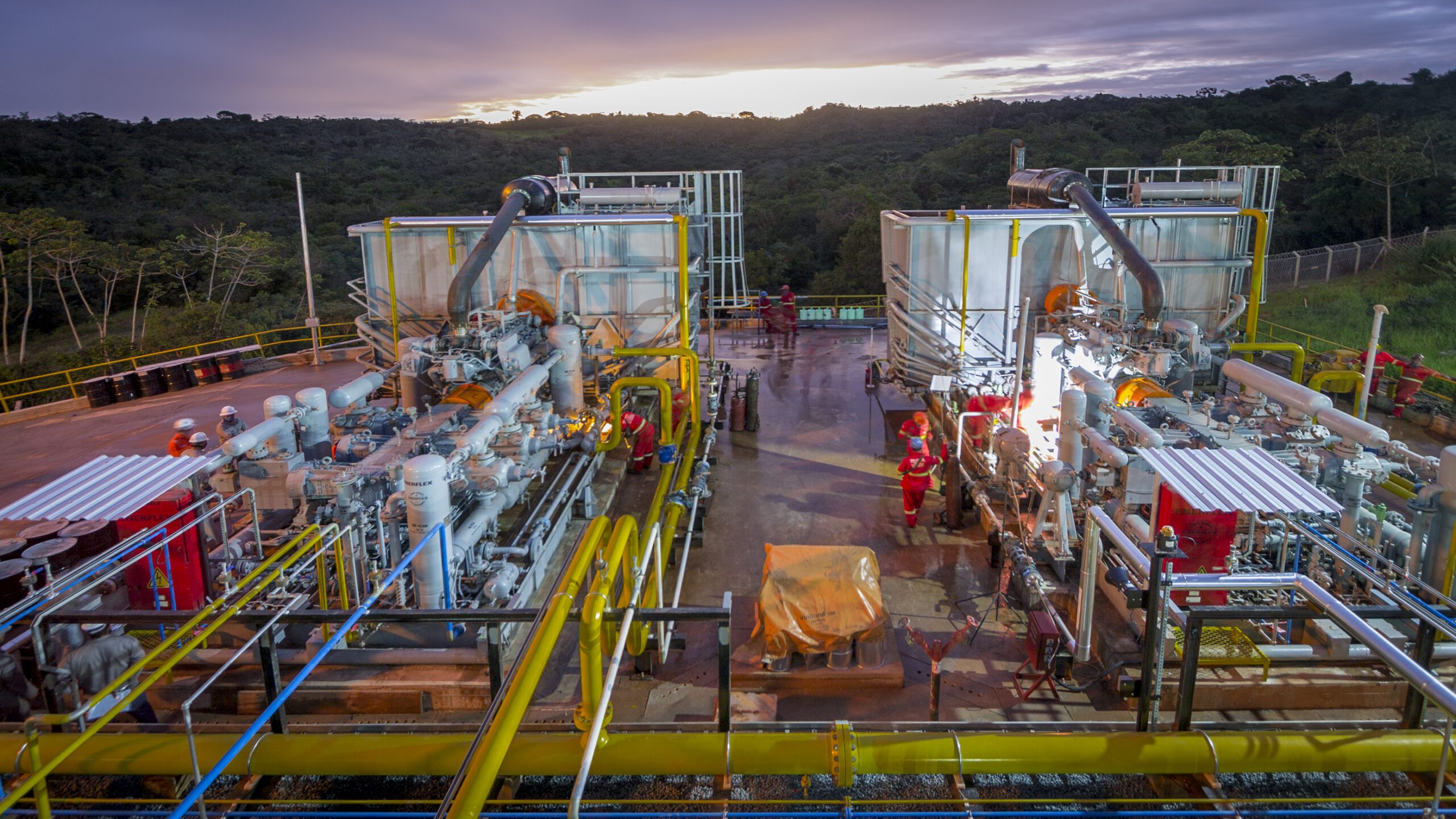
- Mechanical, civil, earthworks, concrete, and structural
- In-house expert technician network
- In-house project and construction management team
- Deep product knowledge mitigates potential on-site setbacks
- Project controls to maintain line of sight on cost and schedule
- Strategic relationships with third-party providers and local contractors
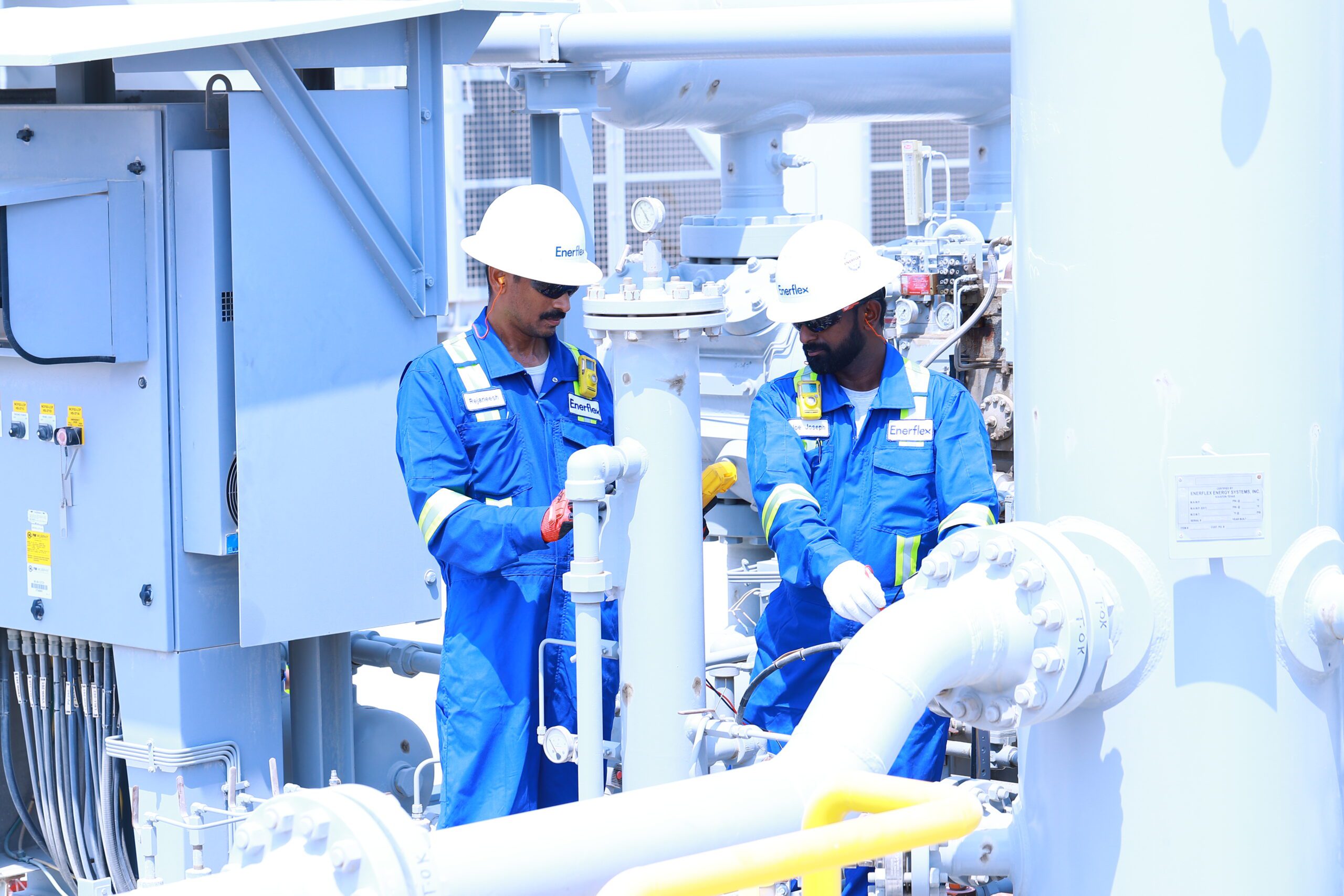
- On-site testing
- Expert technicians available ensuring ease of start-up
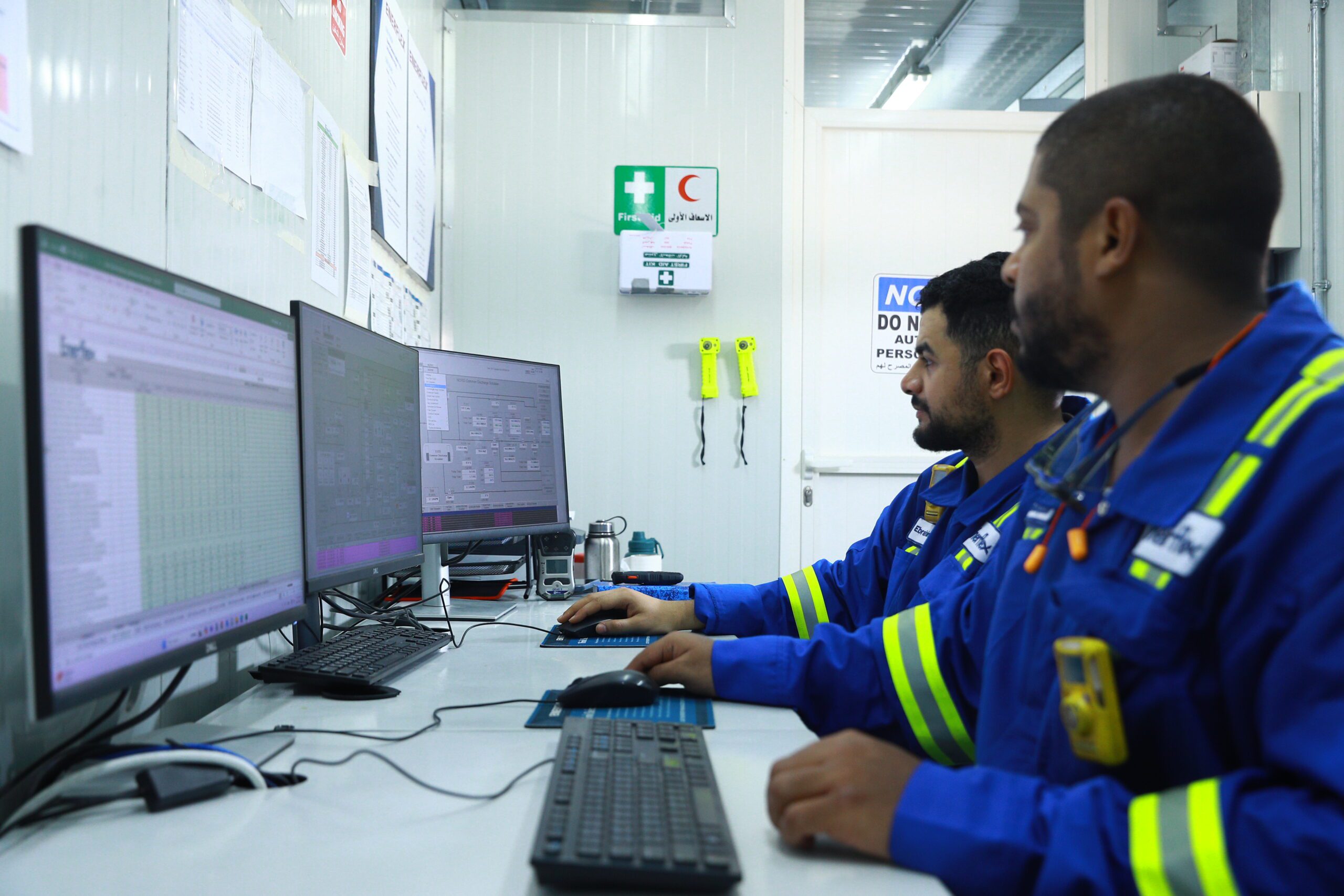
- Day-today plant operations
- Preventative maintenance
- Extensive parts supply
- Major overhauls
The Enerflex Edge
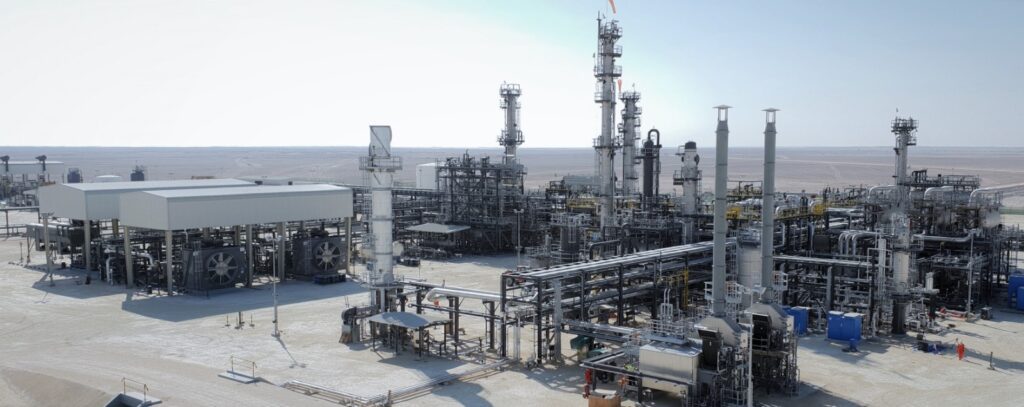
Proven Global Expertise
With a history of successful BOOM projects worldwide, we are known for delivering reliable, profitable solutions designed for local conditions and specific client needs.
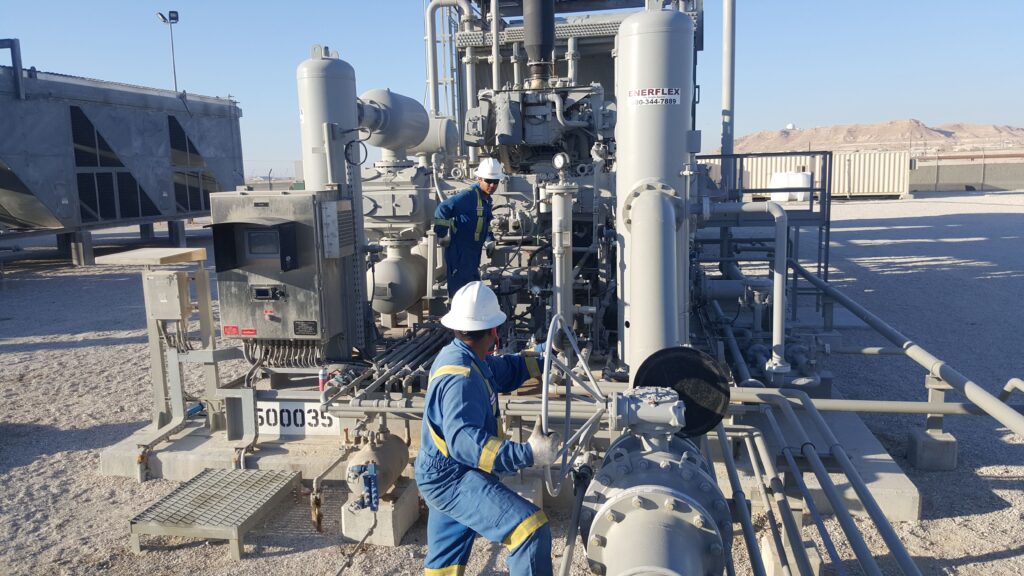
Flexible Financing for Better Value
Our infrastructure financing reduces upfront costs, ensuring an optimal balance between affordability and long-term value for our client partners.
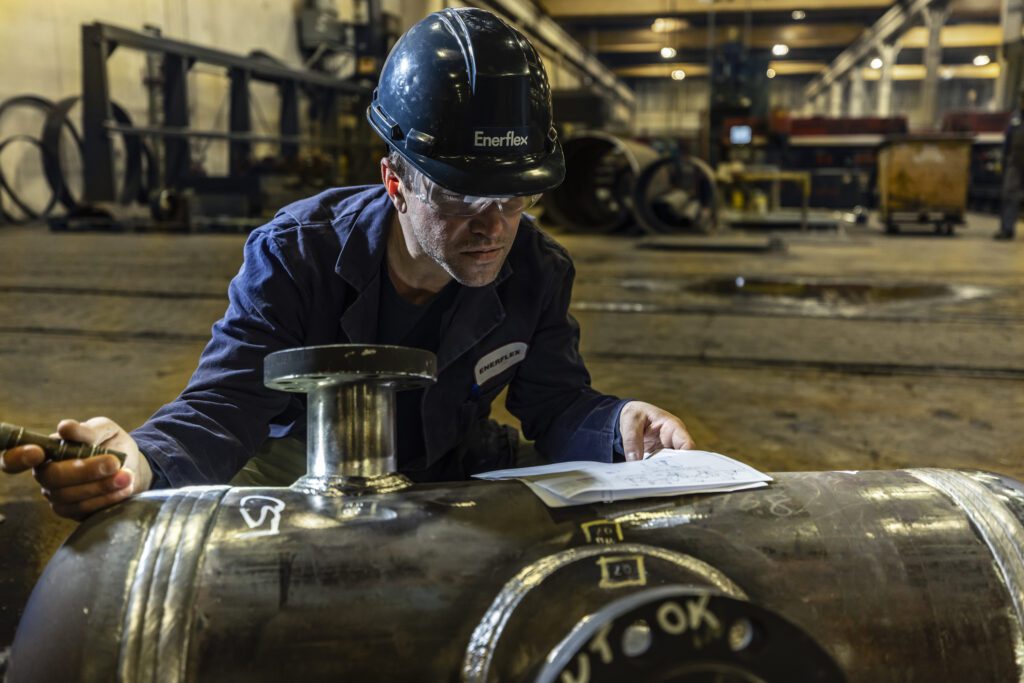
End-to-End Accountability
We handle every aspect of your project—from design to maintenance—allowing you to stay focused on your core business goals while we ensure seamless execution and efficiency.
Proven Energy Infrastructure Solutions
With 26 active BOOM projects and a history of delivering reliable solutions at diverse installations worldwide, we continue to set the standard.
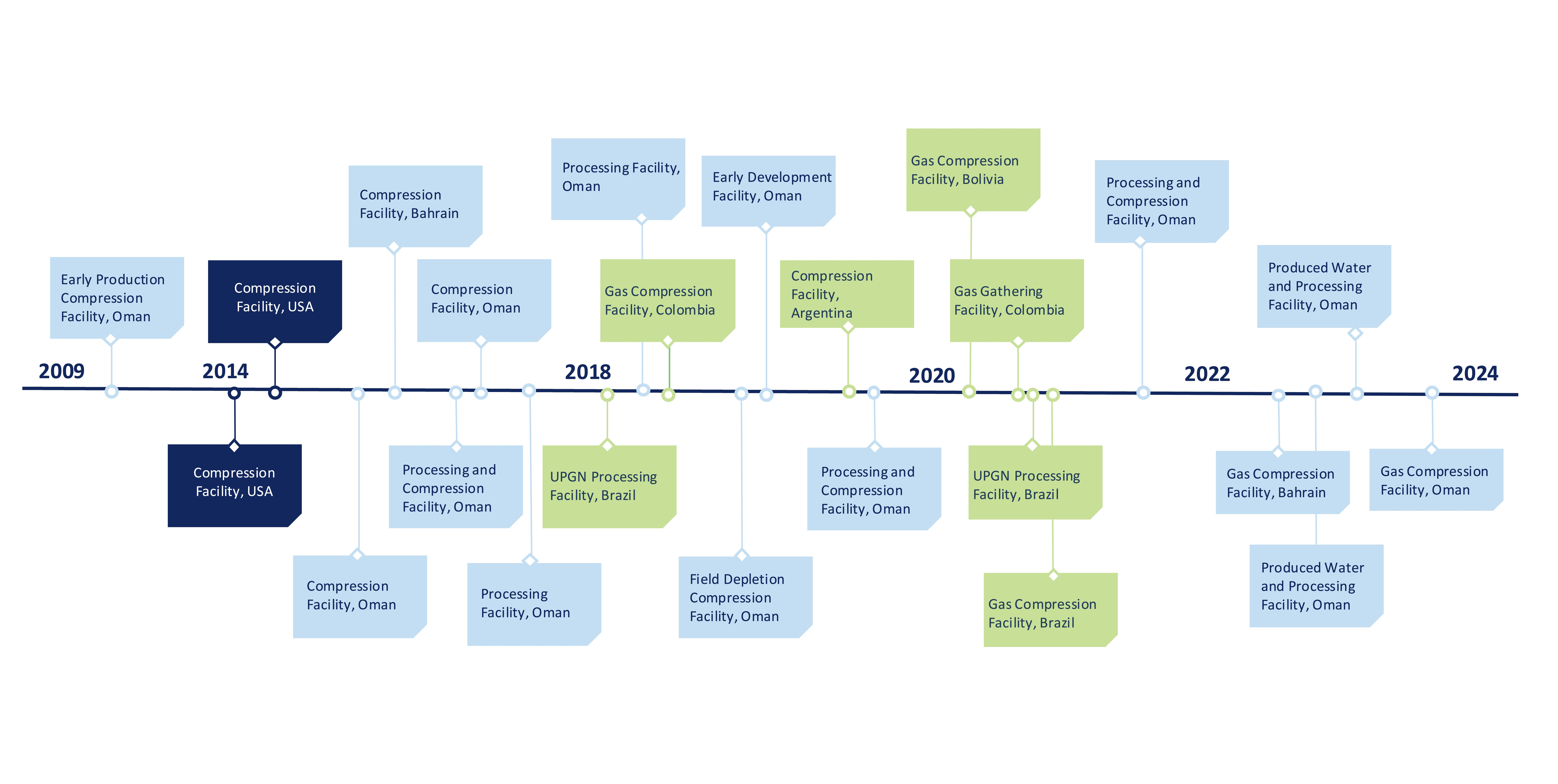
Case Study
42 MMSCFD BOOM Compressor Station
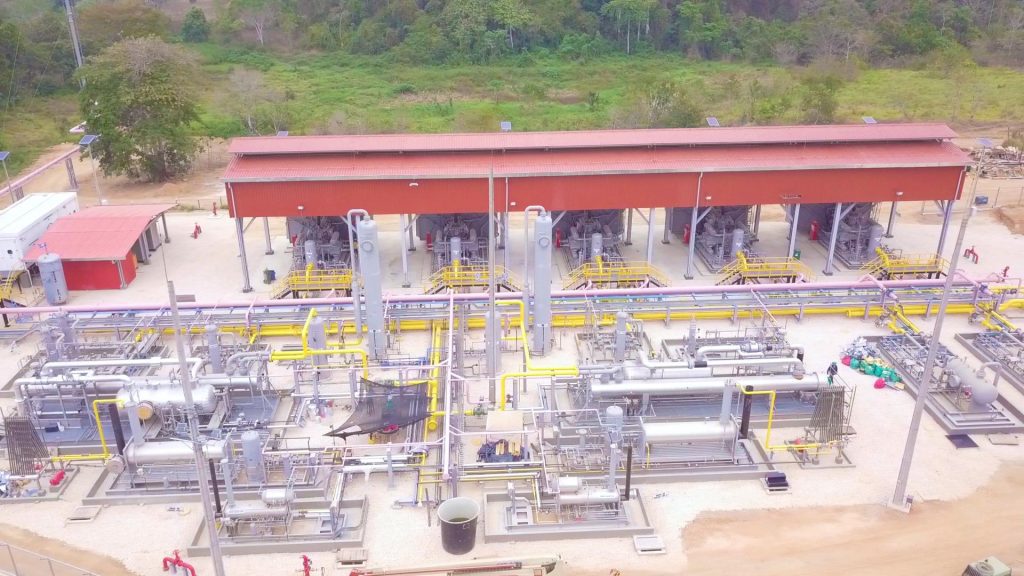
Challenge:
We needed to deliver two 42 MMSCFD gas compression stations, connected by 30 km of 6-inch flexsteel pipeline, within an ambitious 40-week timeline. The project required retrofitted fleet compressor packages and fully integrated standalone stations with compression, gas generation and safety systems.
Solution:
We provided a turnkey BOOM solution: engineering, manufacturing, commissioning, and testing. The stations featured Waukesha 7044 engines with Cooper MH series compressors. The flexsteel pipeline connected the stations to Colombia’s national gas network.
Outcome:
Completed on time and within budget, the project received full HSE recognition. The flexsteel line now links the gas plant to critical national infrastructure along Colombia’s Caribbean coast. Over 200,000 man-hours were worked with zero lost-time incident.
Discover More About Our Products and Services
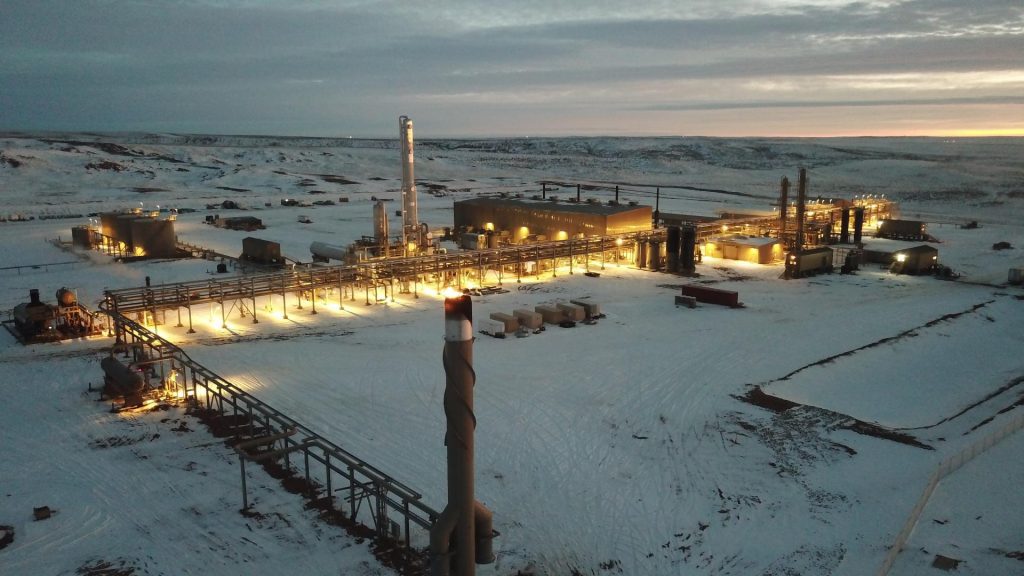
Cryogenic / Deep Cut
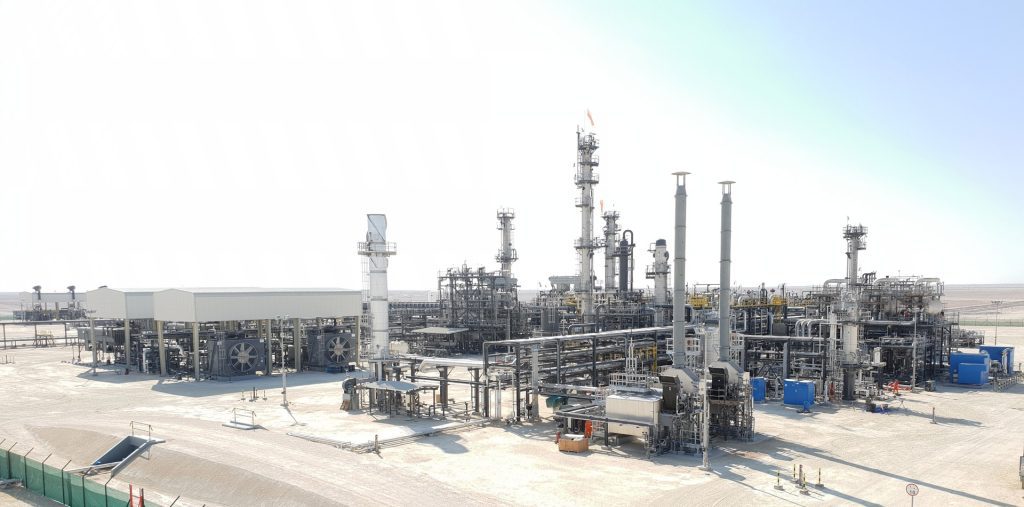
Gas Processing
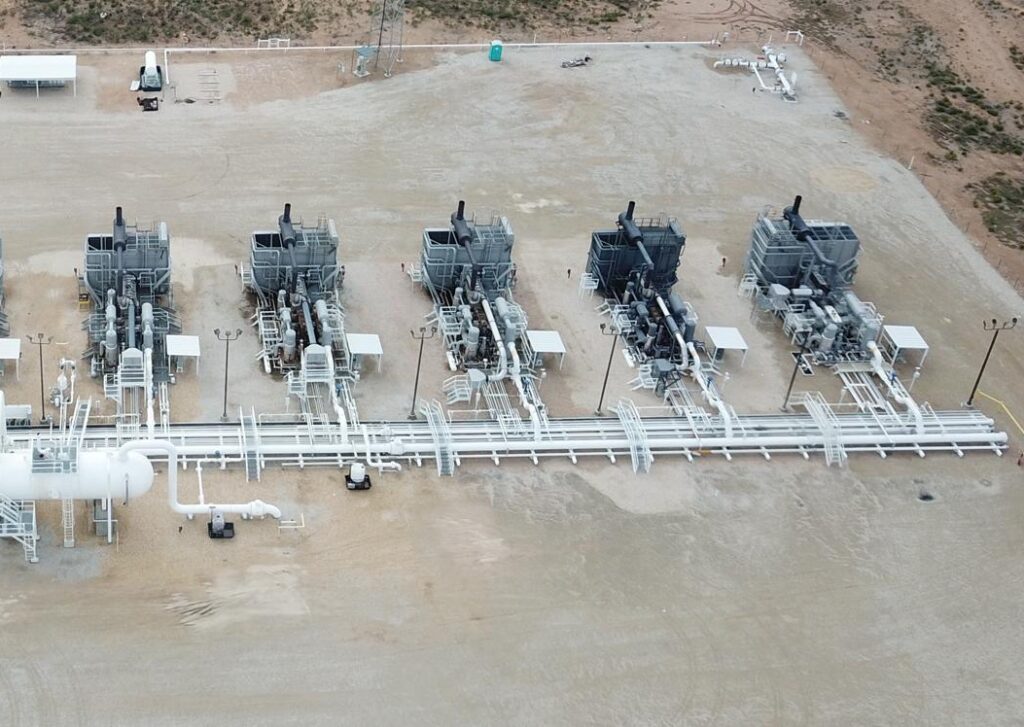