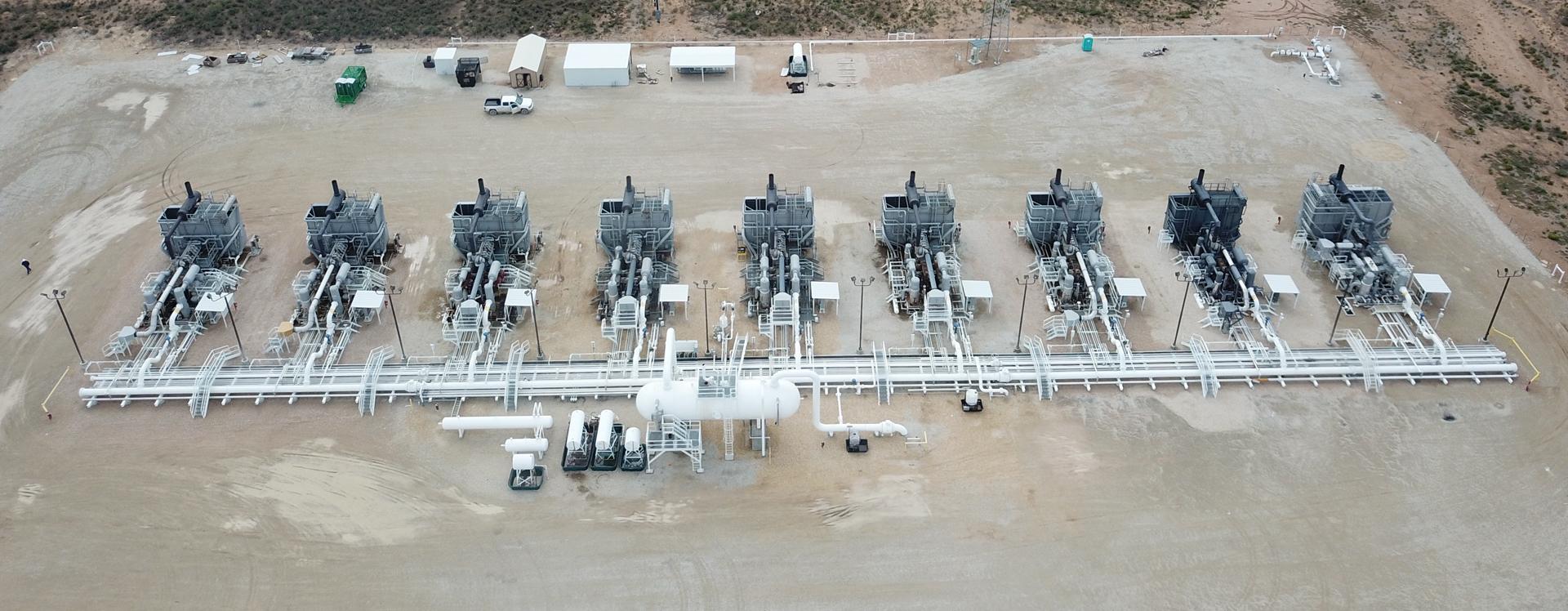
Equipment
Compression
Fast solutions. Quick returns. Reliable performance.
For over four decades, we’ve delivered flexible gas compression solutions that prioritize speed and cost efficiency. Our streamlined processes enable rapid deployment and reliable performance, driving faster returns for your business.
The Enerflex Edge
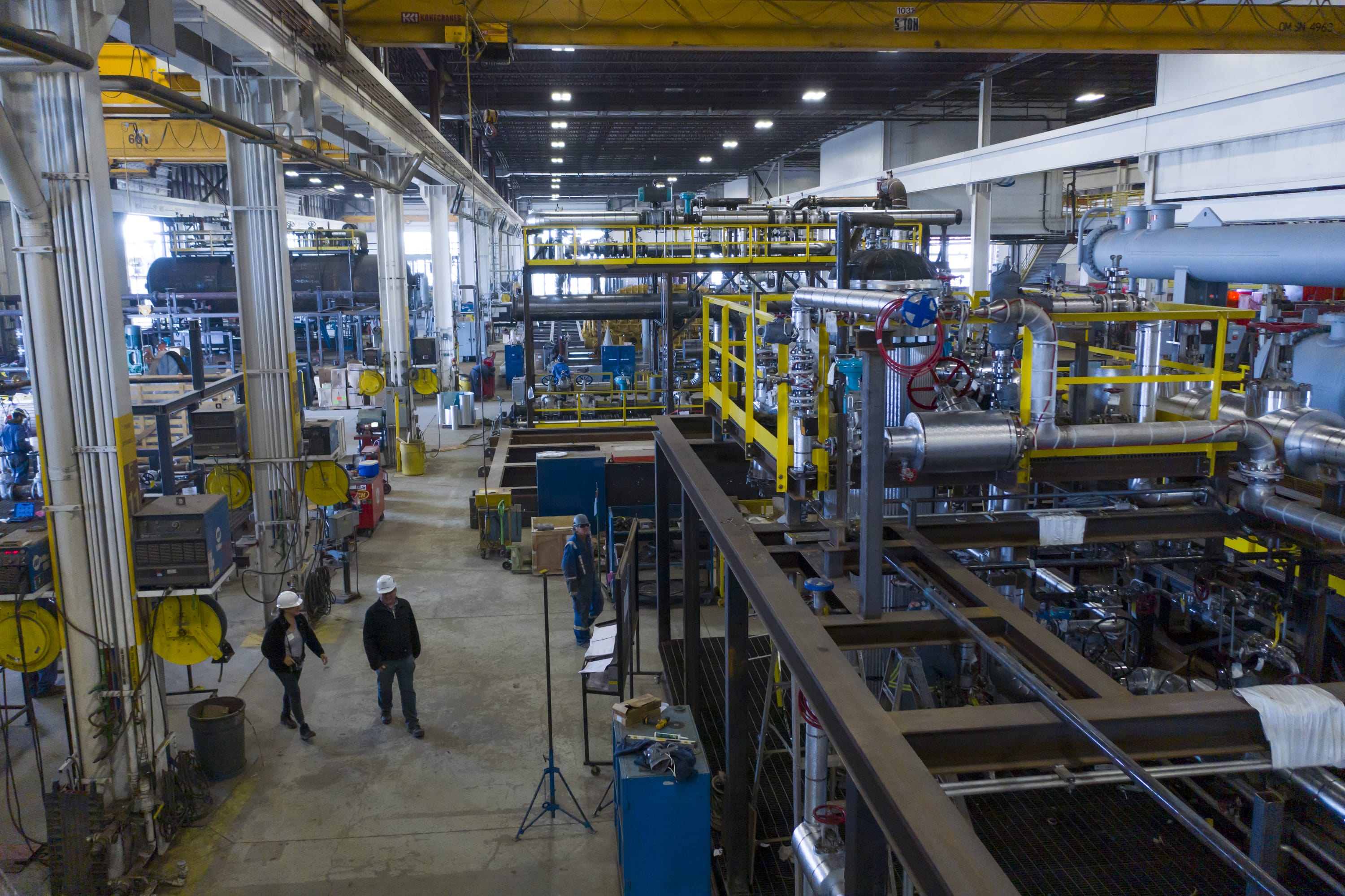
Speed to Market with Lean Manufacturing
Our lean manufacturing practices allow us to move faster than others. With streamlined workflows and advanced technology, we ensure fast turnaround from design to deployment—helping our partners get operations up and running sooner.
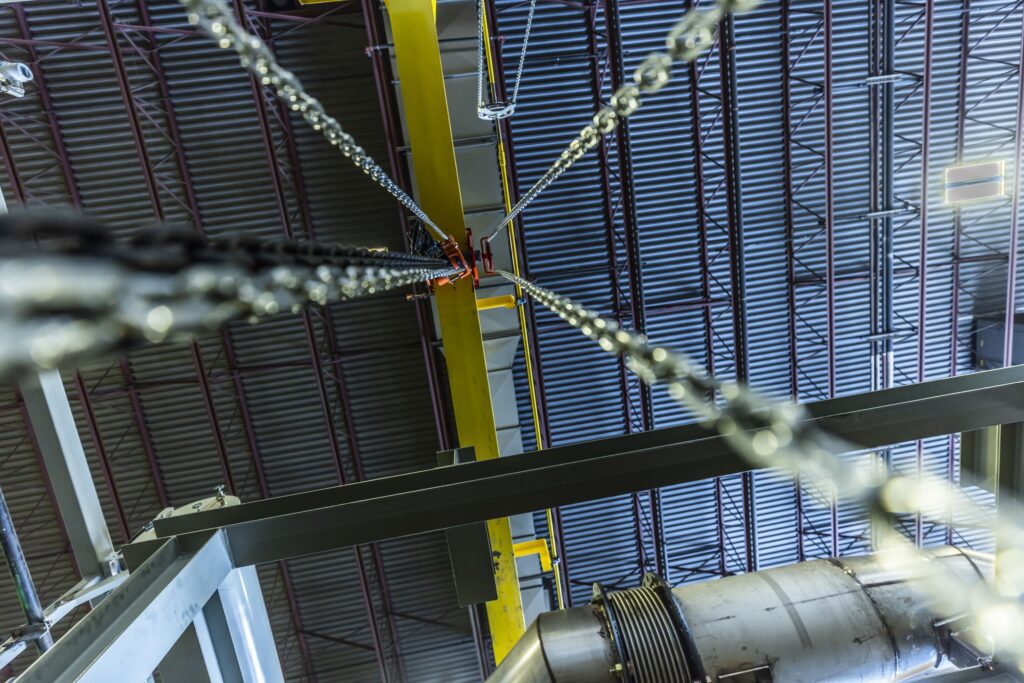
Strong Supply Chain and Service
Thanks to strong partnerships with key suppliers, Enerflex can access critical equipment, engines, and parts quickly, ensuring faster time to market. Combined with a global network of service hubs, we efficiently deliver cost-effective solutions that keep your operations running smoothly.
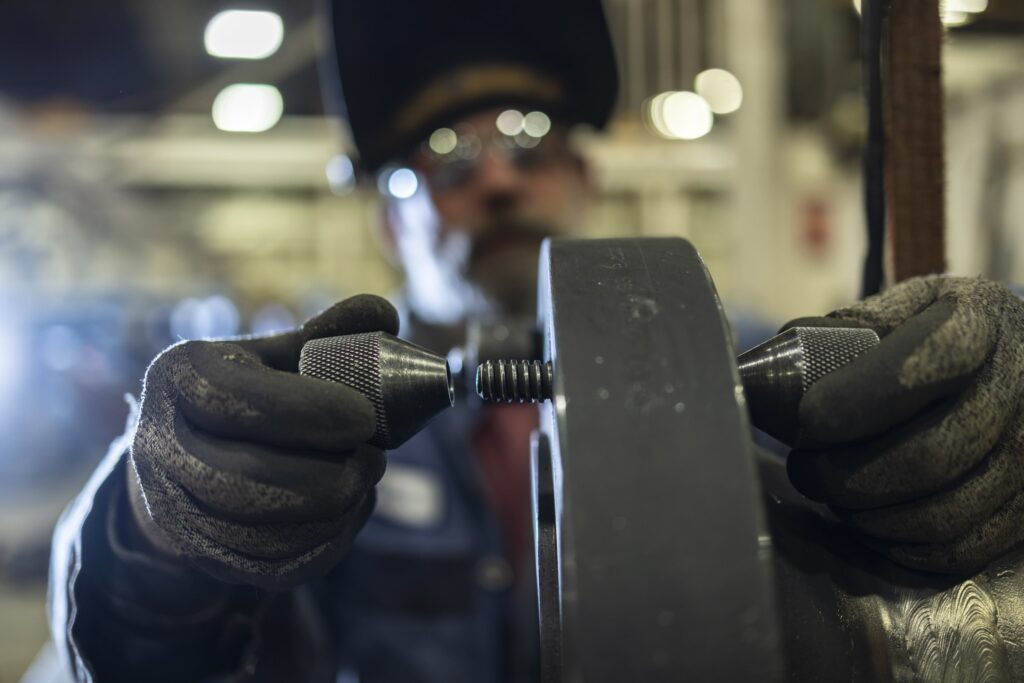
Expertise Every Step of the Way
We support you from design to installation and throughout the life of your compression system. Our service teams know the equipment inside and out, offering seamless commissioning, quick repairs, and unparalleled support. This end-to-end expertise ensures minimal downtime and maximum reliability.
1.5MM
Horsepower of gas compression operated by Enerflex
10K+
Compression solutions installed
710K
In-house manufacturing capacity
45
Years’ expertise building compression solutions for a variety of applications
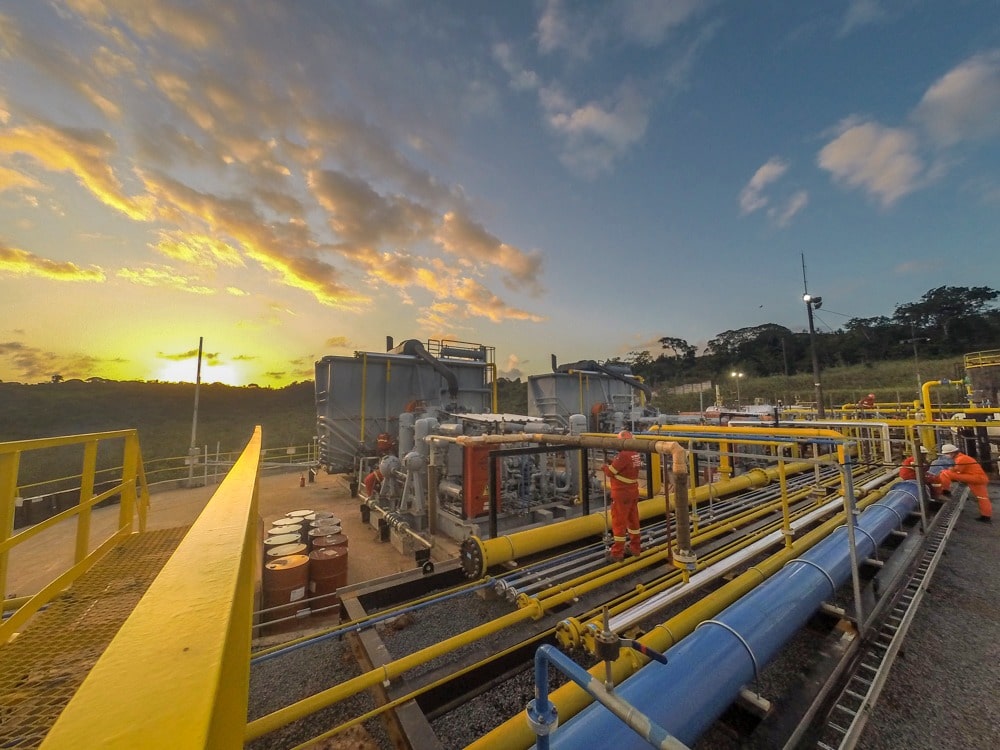
Custom Compressors
Enerflex offers fully custom compression packages ranging from 20 HP to 10,000 HP, built to meet the unique demands of each project. Whether operating in sub-Arctic cold, tropical heat, or extreme desert conditions, our solutions excel in complex environments. We tailor each unit to fit the type of gas, environmental conditions, and operational challenges, providing superior performance and flexibility.
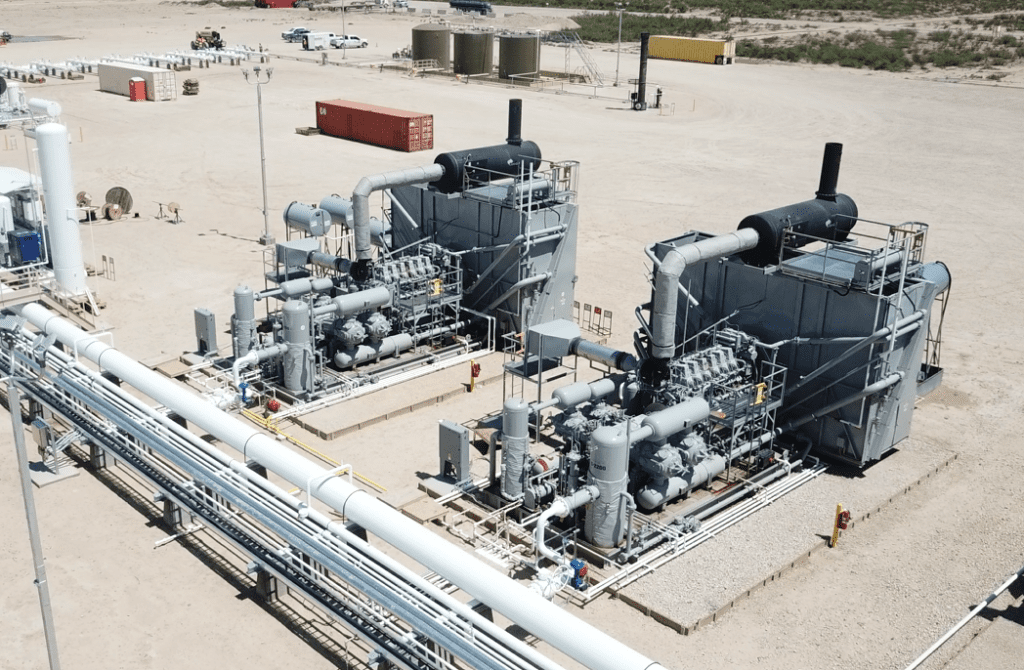
Pre-Engineered Compressors
We provide off-the-shelf packages for fast deployment, leveraging proven manufacturing and economies of scale for cost savings and quick turnaround times. Upgrades and custom options are then engineered to meet our partners’ specific standards. With in-house commissioning and after-market services expertise, we ensure efficient, streamlined installation and reliable performance.
Case Study
13,000 HP Compression Station
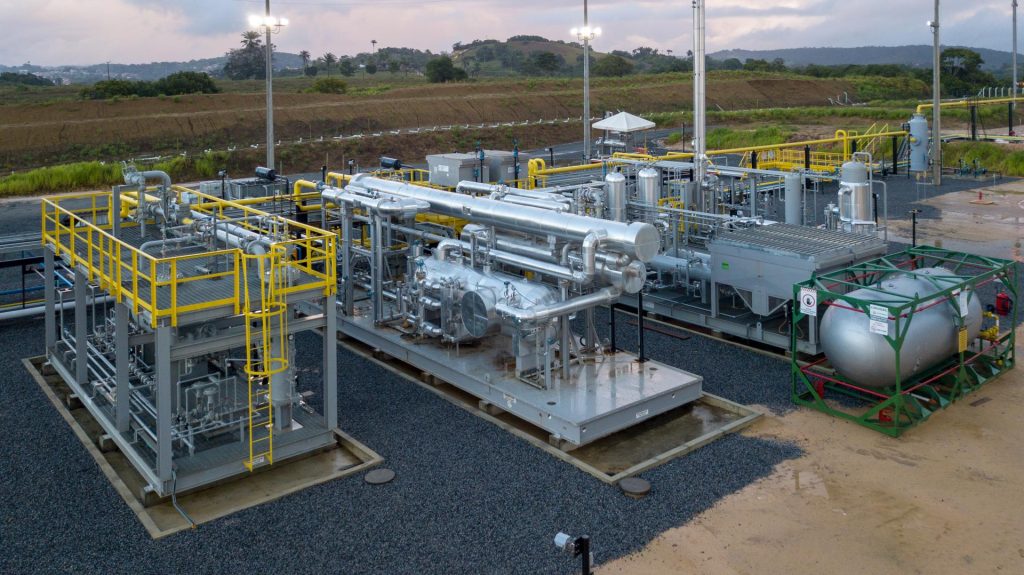
Challenge:
Enerflex needed to deliver a solution to provide fuel gas to a large power-generating facility in Tapinhoa, Brazil. The project required the construction of a 13,000 HP pipeline booster station on a hilltop, with extensive grading to create a suitable space.
Solution:
Three 4,500 HP compression packages, with full civil, mechanical, and electrical engineering, along with design, installation, and commissioning.
Outcome:
Enerflex completed the project on- time and within budget, delivering a fully operational plant in just 210 days from purchase order to plant acceptance.
Electrification
Enerflex has been a leader in electrification for decades, with over 3 million horsepower of electric-motor compression installed globally. Our e-compression solutions reduce exhaust emissions by switching to electric motor drives. With offerings like solar self-generation and battery energy storage systems, we help our partners while improving runtime and lowering costs.
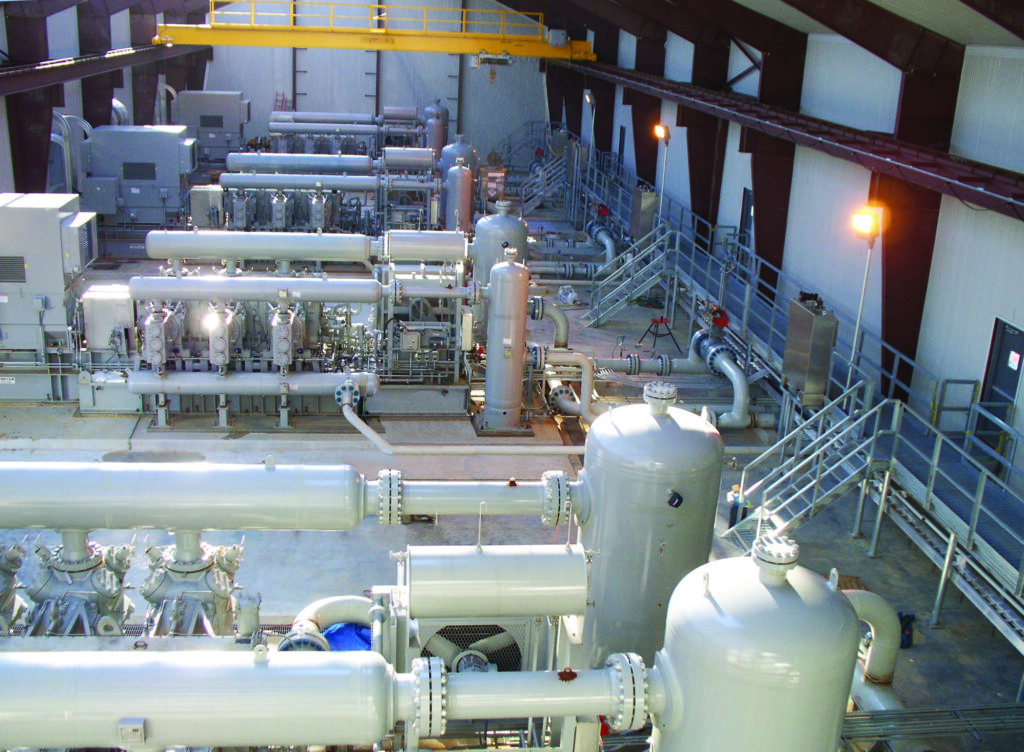
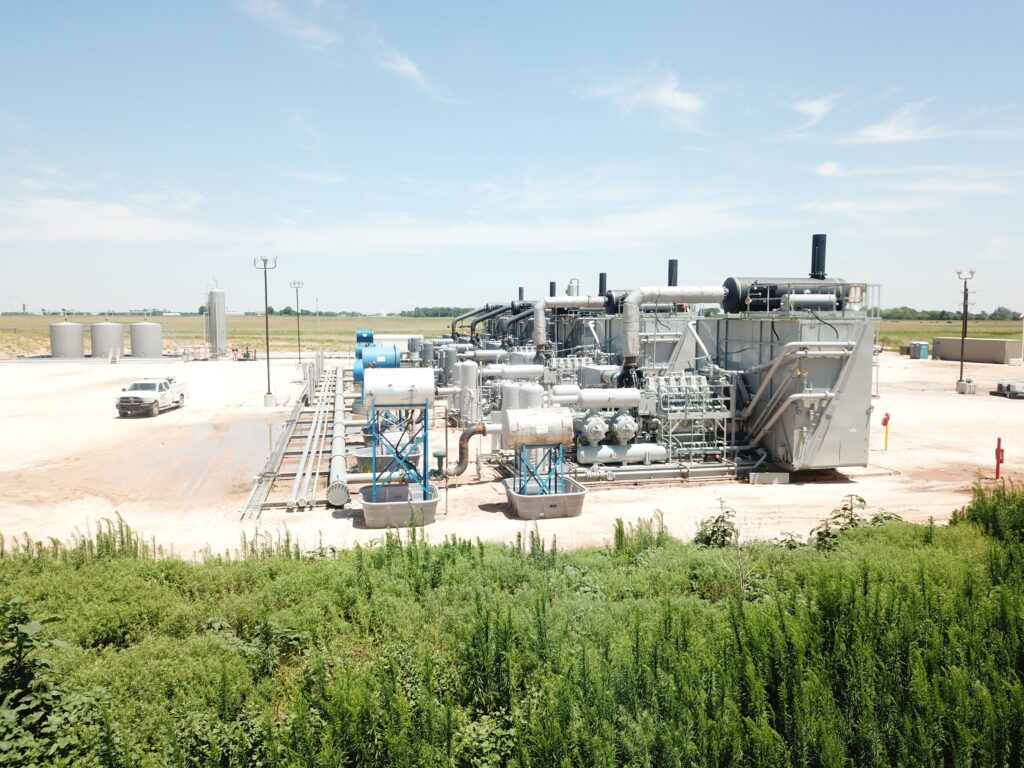
Contract Compression
With a large inventory of field-ready assets, we provide equipment ranging from 95 HP to 64,000 HP, available for rapid deployment. Our Contract Compression model allows for scalable, long-term solutions that fit your specific process needs, supported by experienced technicians.
Certifications
Our equipment always meets stringent industry compliance standards.
- API 619 Oil Flooded and Dry Screw Compressors
- API 617 Packaged Centrifugal Compressors (Chapter 2 and 3)
- API 618 Packaged Reciprocating Compressors
- European Union’s ATEX and PED Directives
- CE Markings for European Code Requirements
- EAC
- ASME VIII
- NEC
- CSA
- API
Discover More About Our Compression Systems
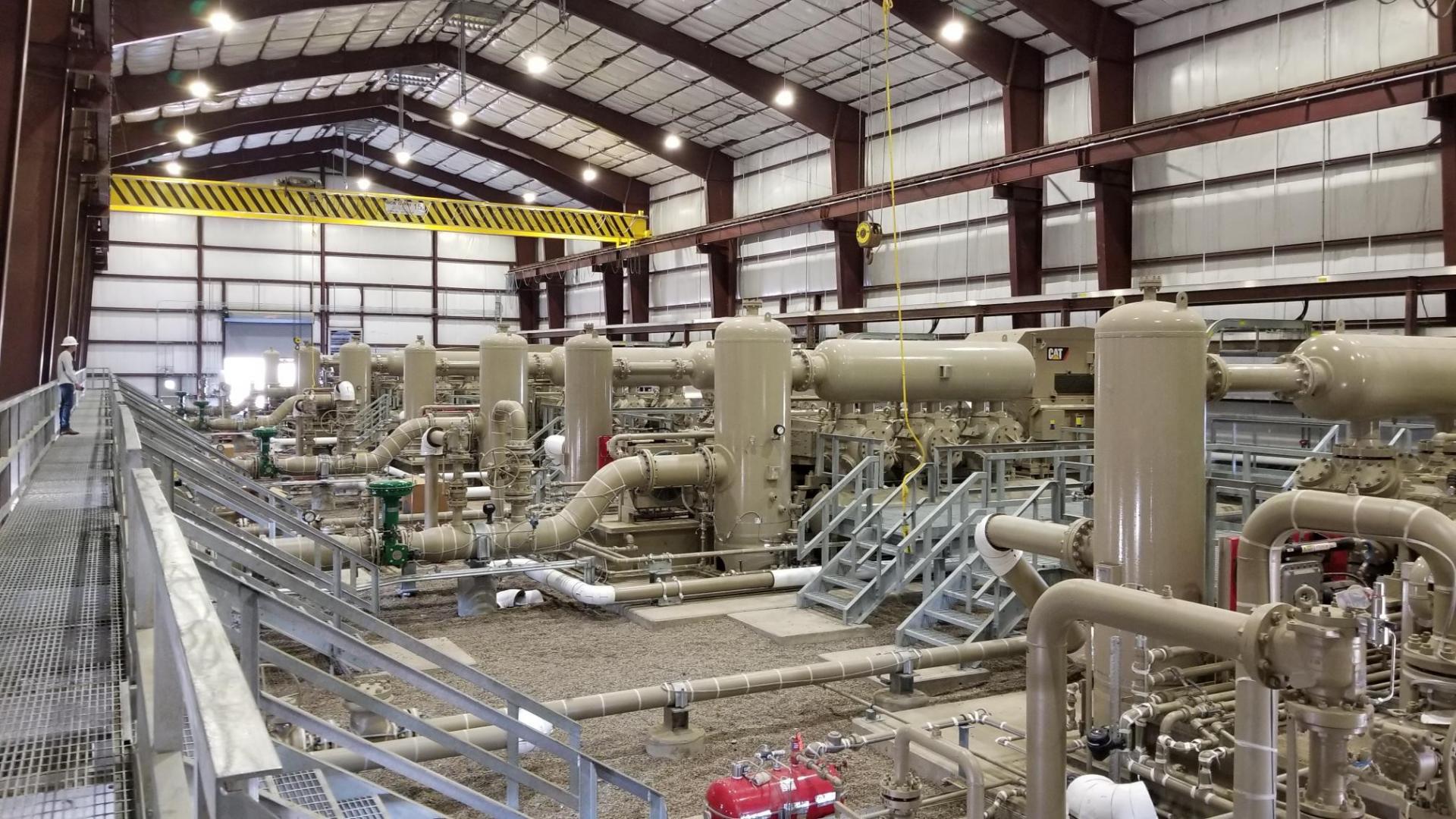
Reciprocating Compression
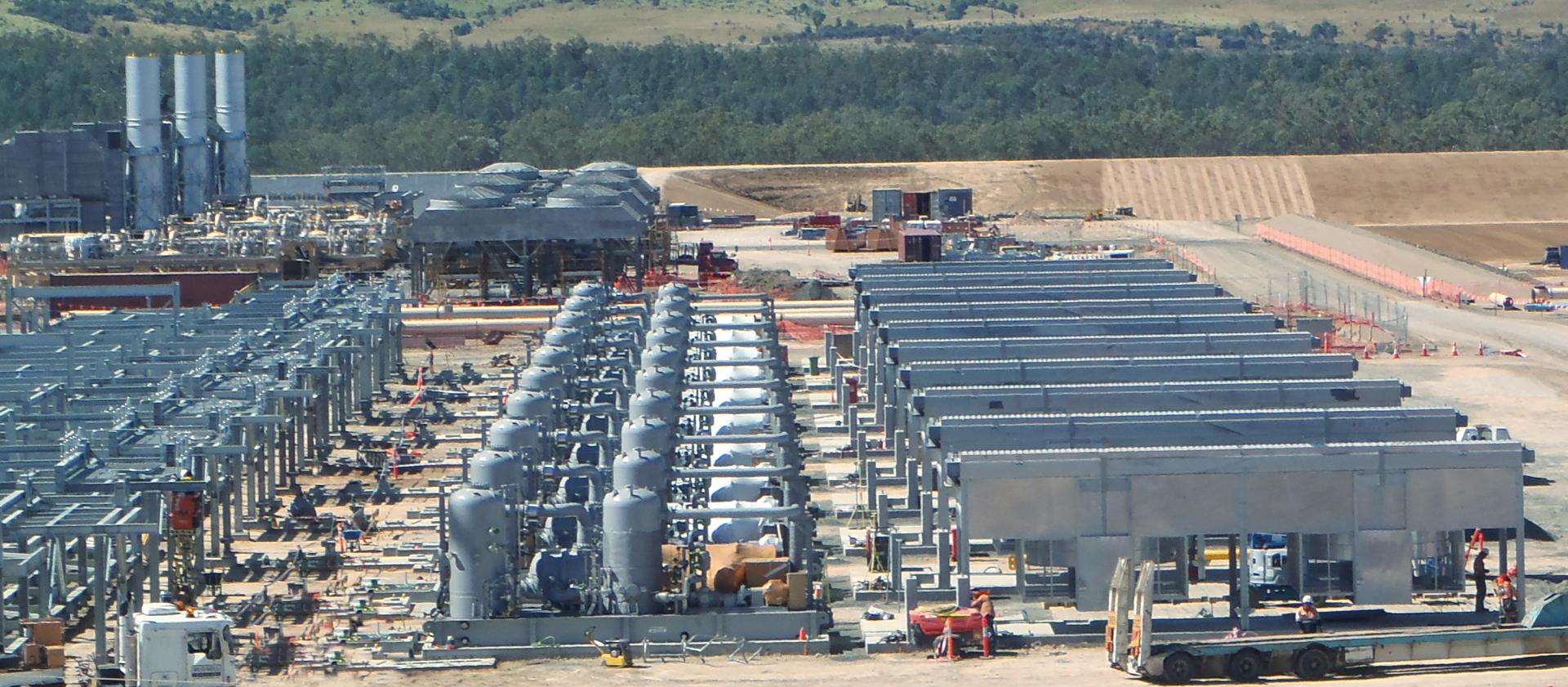
Rotary Screw Compression
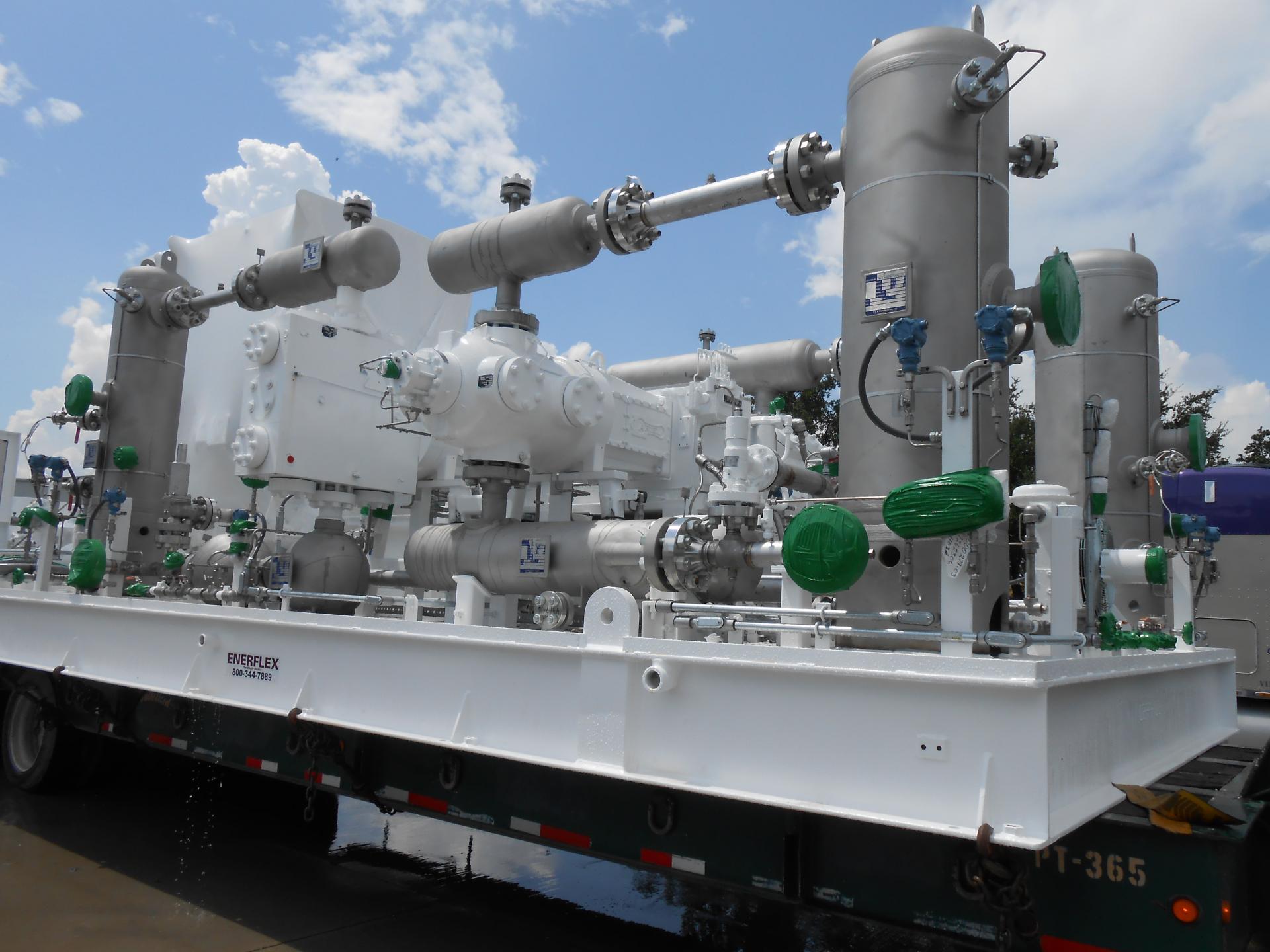