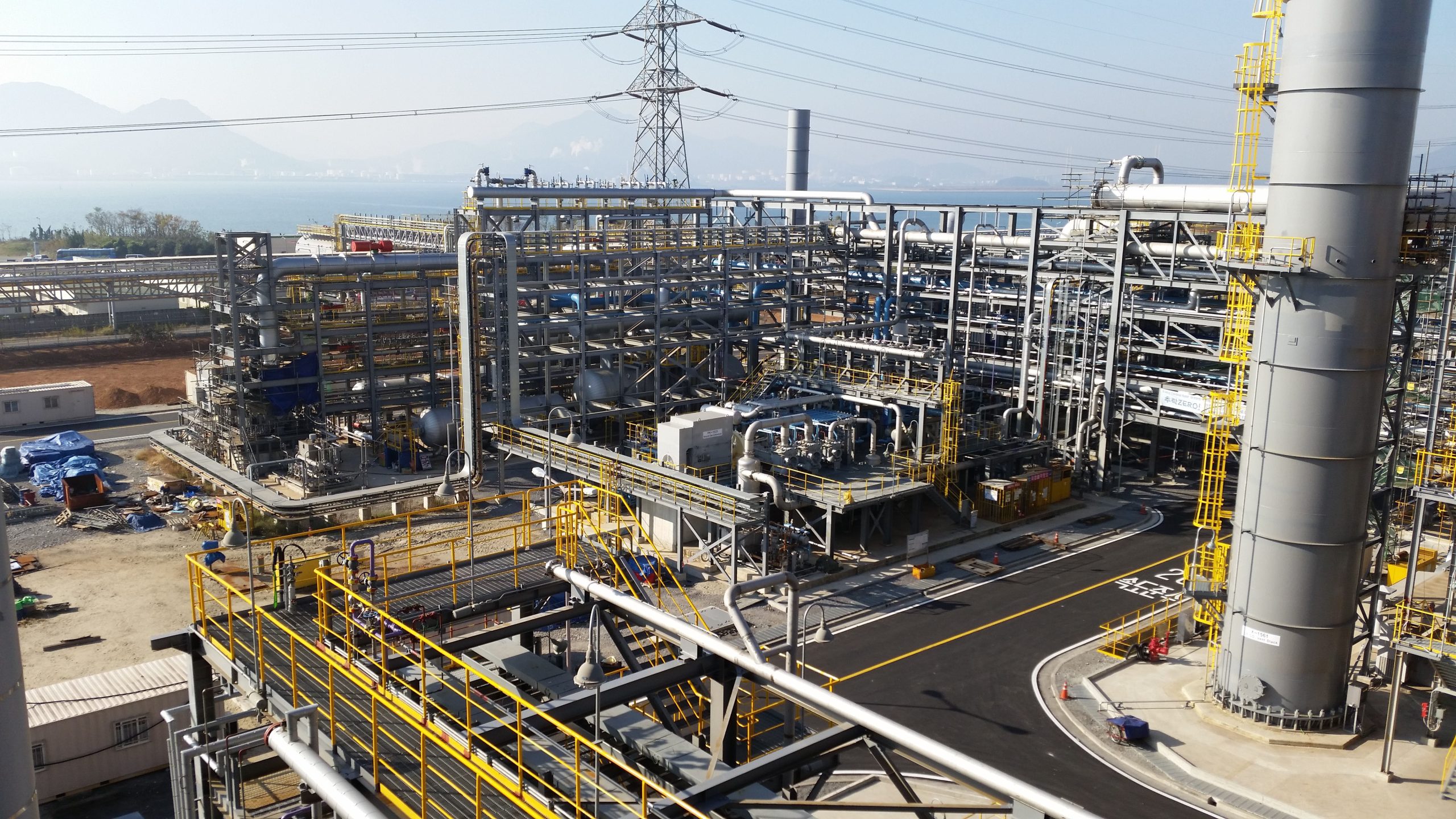
Equipment
Refrigeration
Tailored Refrigeration Solutions for Every Industry
Enerflex delivers expert refrigeration solutions worldwide. Our end-to-end approach ensures timely, cost-effective results, backed by decades of experience in deploying efficient, scalable refrigeration systems.
The Enerflex Edge
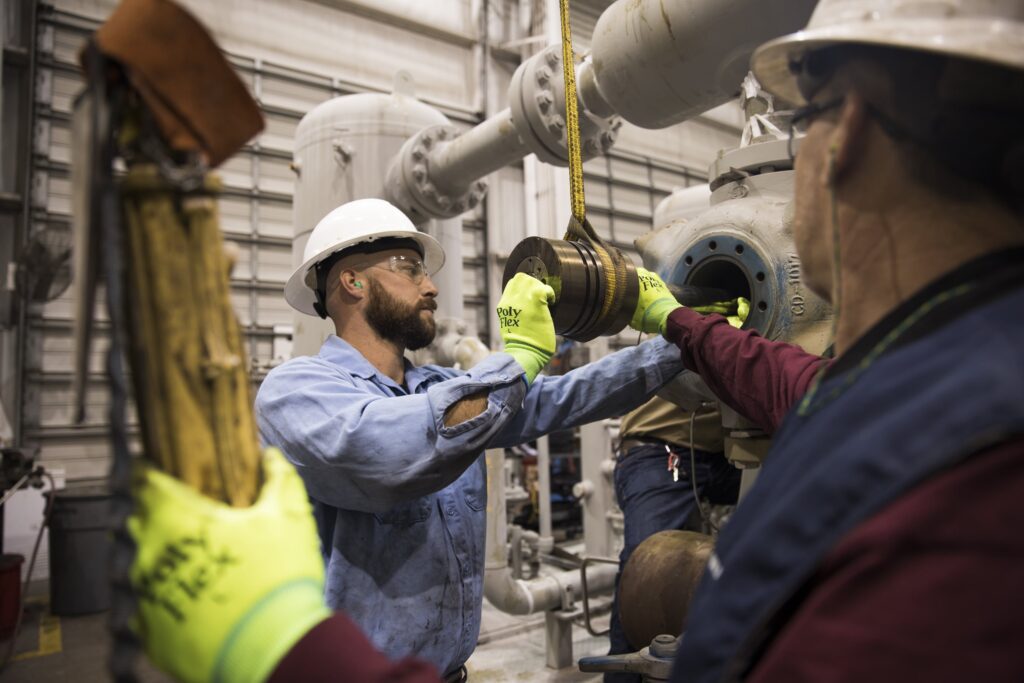
Modular Design with Shop-Trial Fit
Our large-scale facilities allow for full trial runs and test fits before shipping equipment to your site, reducing on-site setup time and improving operational readiness from day one.
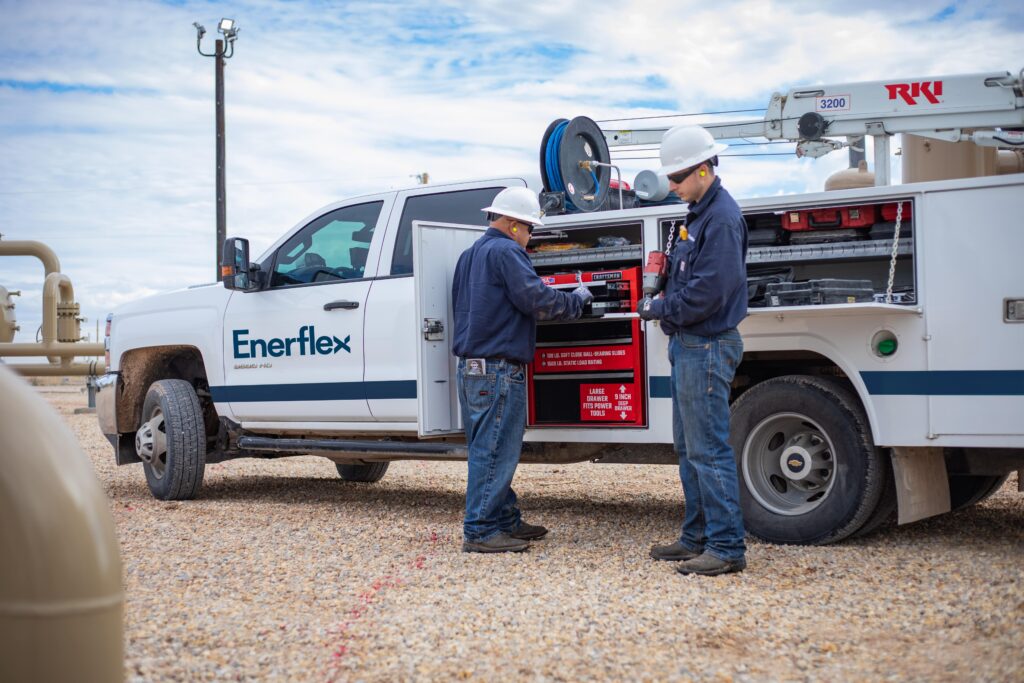
Expert Technicians Provide Comprehensive Support
Our skilled service technicians bring extensive experience in refrigeration equipment. With access to OEM parts and preventive maintenance programs, we offer seamless operations and extended equipment life.
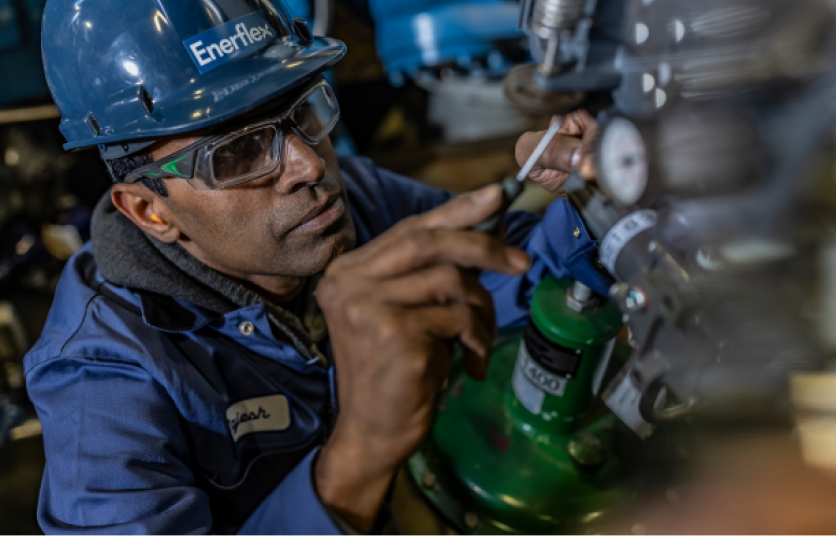
Tailored Solutions
We partner with OEMs to provide flexible, cost-effective solutions designed for your needs. With expertise in rotary screw, reciprocating, and centrifugal technologies, we ensure the right fit for every application.
4+
Types of specialty refrigeration systems, including hydrocarbon, freon, ammonia, and CO2
10
Minimum tons of refrigeration per unit
20,000
Maximum tons of refrigeration per unit
-150°F
Lowest temperature handling
Refrigeration Solutions for Every Project Size
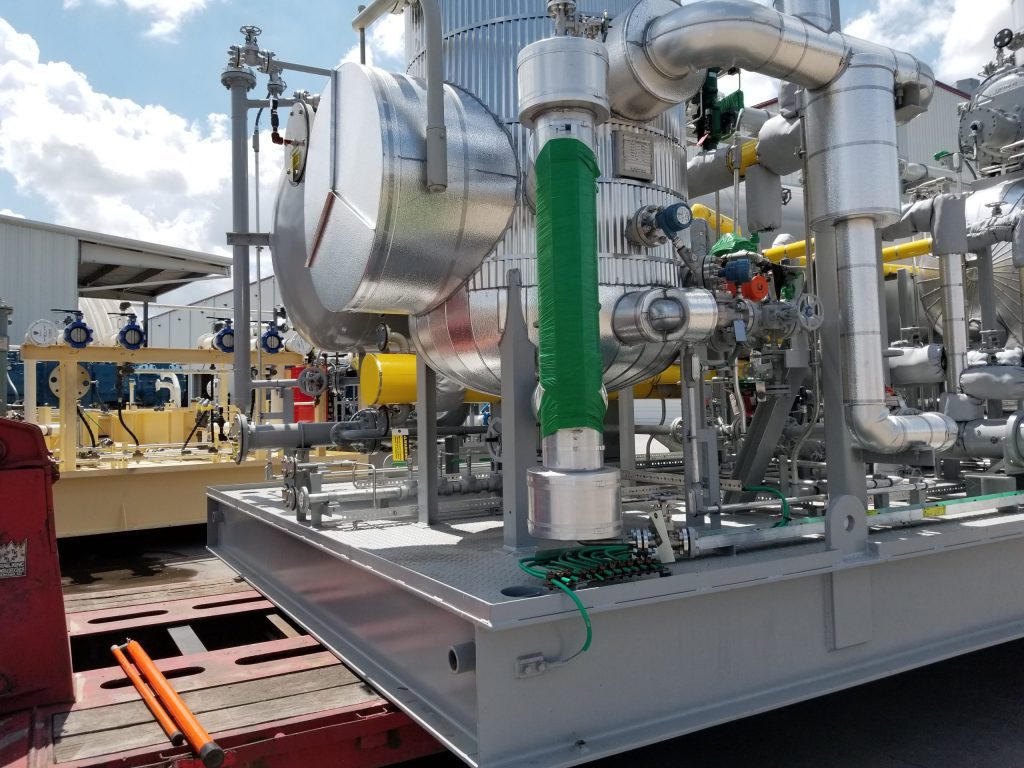
Skid-Mounted Units for Smaller Systems
Our skid-mounted units offer a fully assembled, compact solution for smaller-scale applications. These single or multi-skid systems minimize on-site installation with all interconnecting piping pre-assembled, ensuring fast, efficient installation and reliable performance.

Fully Modular Units for Larger Systems
Our fully modular systems are designed to streamline large-scale projects by breaking them into sub-modules that are match-marked for easy reassembly in the field, easing on-site installation, improving construction scheduling, and optimizing for operational safety.
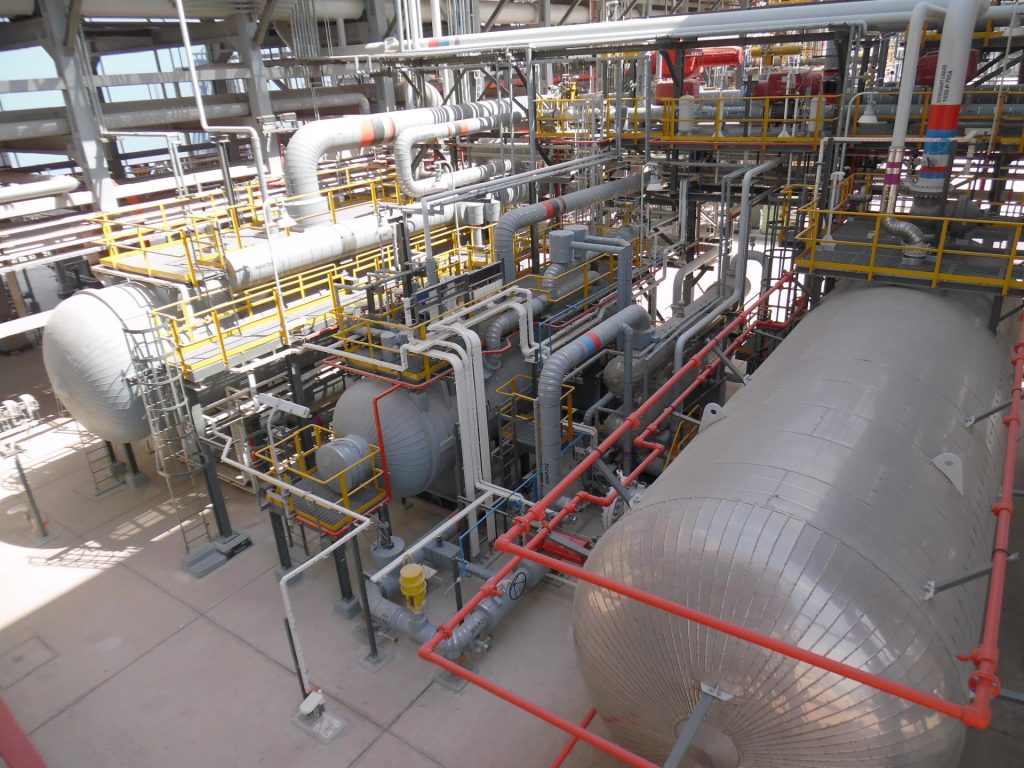
Stick-Build Designs for Extremely Large Systems
Our stick-build refrigeration systems are tailored for the most complex, large-scale projects. With full in-house engineering and design capabilities, we deliver end-to-end solutions that meet the demands of massive, high-performance applications worldwide.
Refrigeration Applications
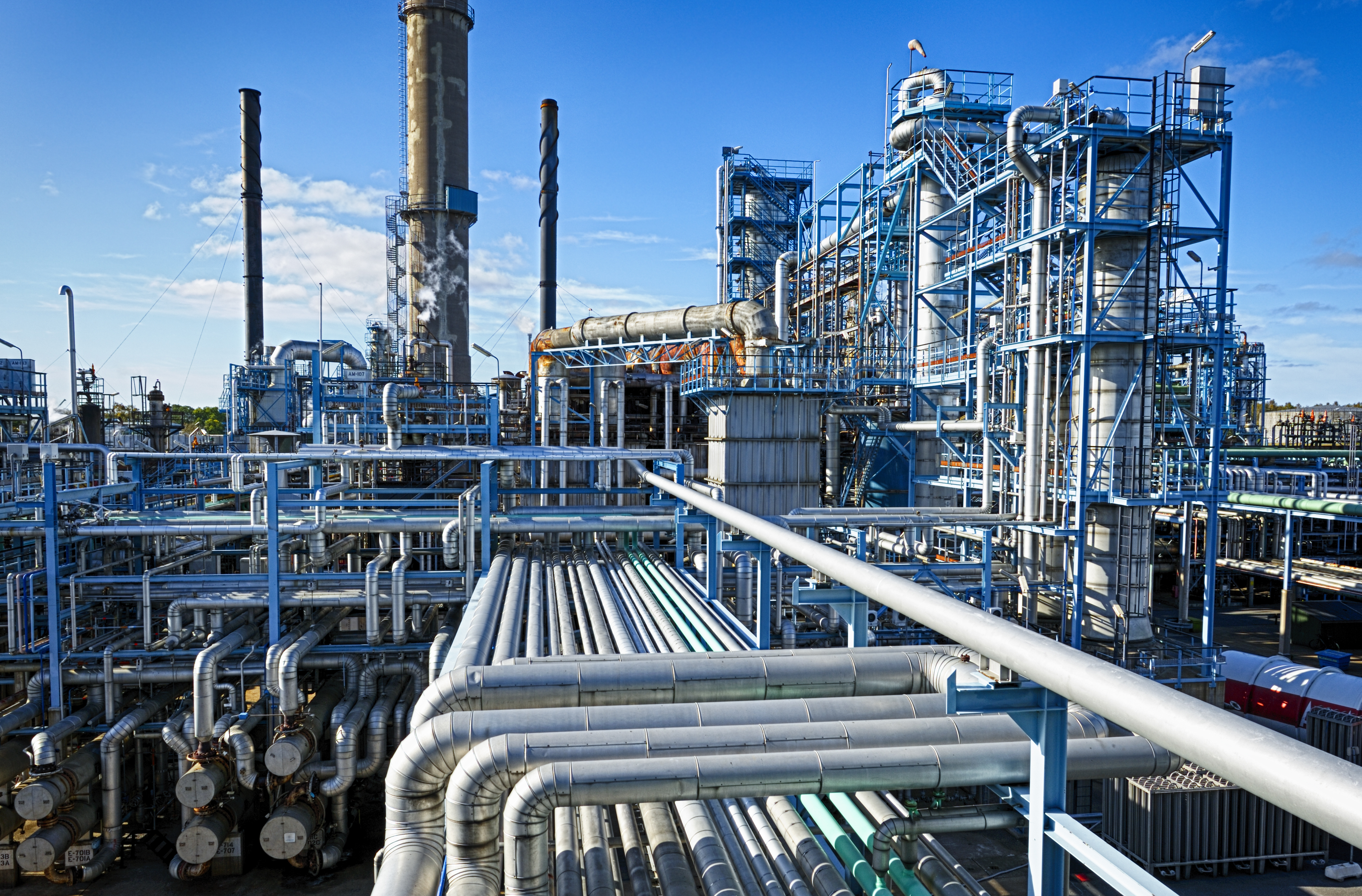
Export and Import Terminals
Enerflex designs LNG, LPG, and olefin export/import terminals, offering equipment like metering skids, pumps, and loading arms, plus engineering and feasibility studies.
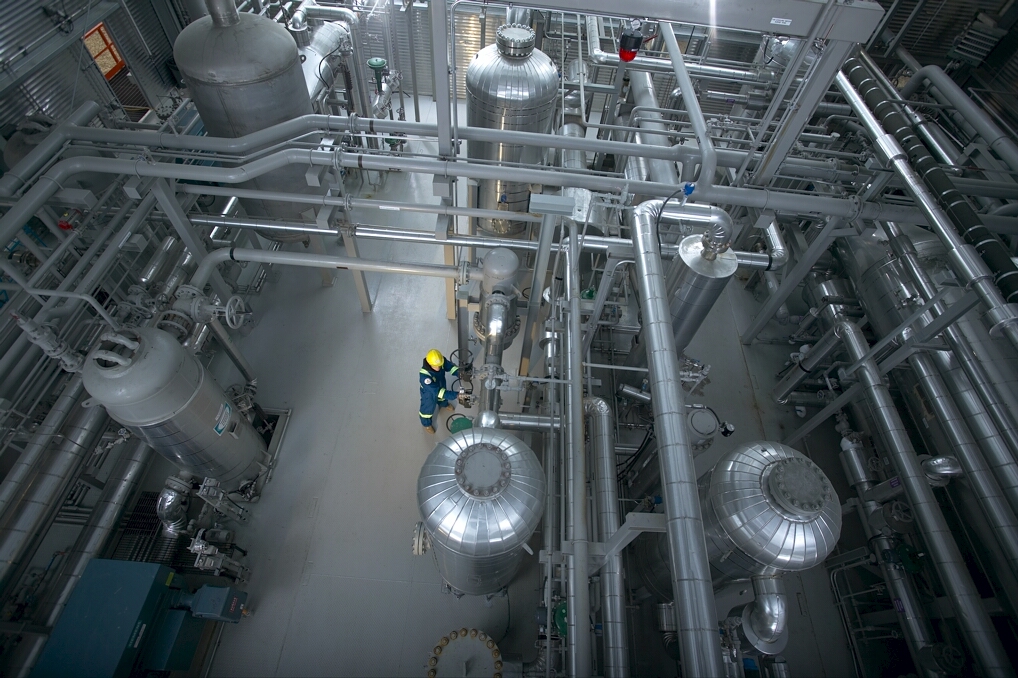
CO2 Liquefaction Plants
We provide complete liquid CO₂ systems for both food and non-food grade applications, sourcing from ethanol plants, amine installations, pipelines, and more.
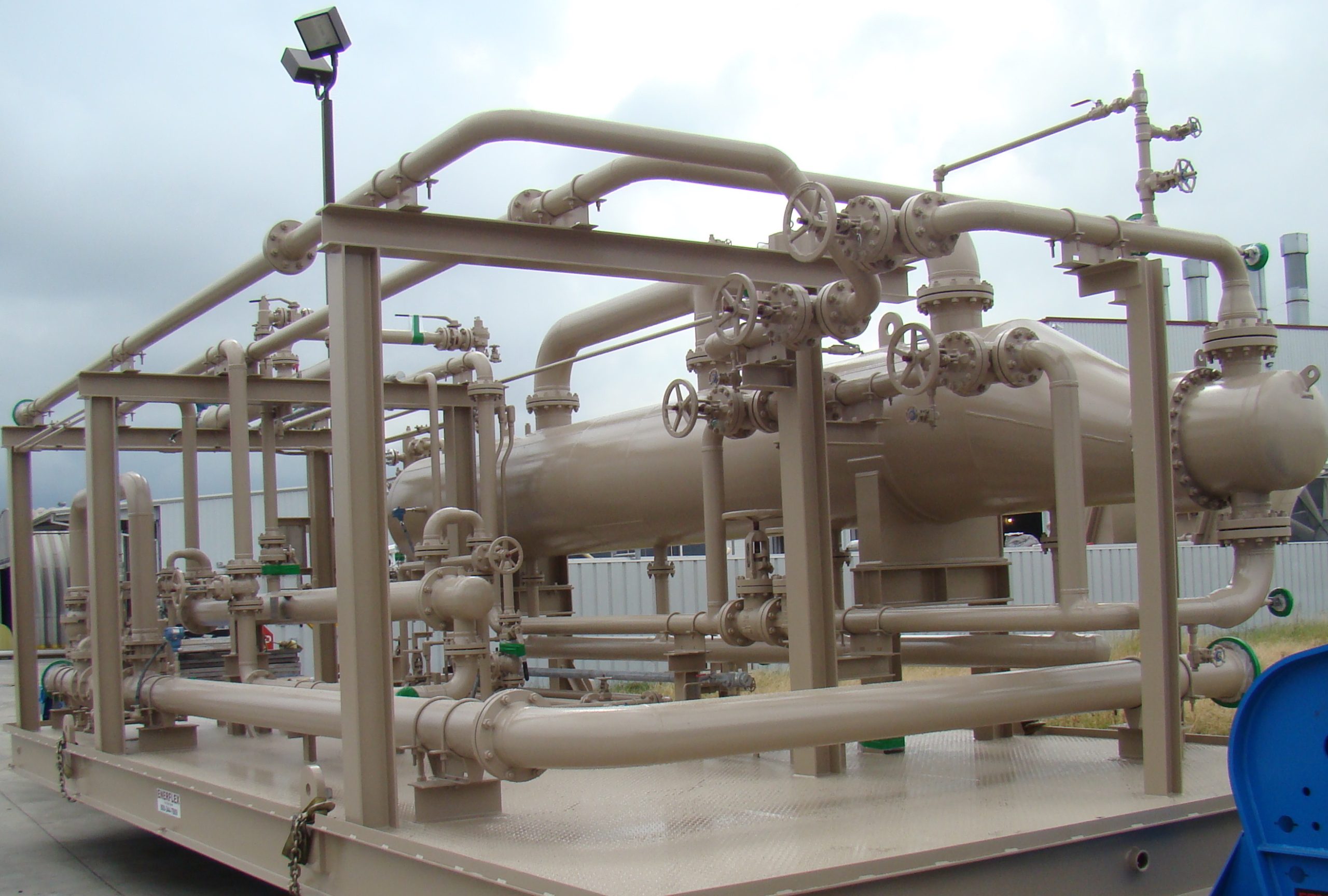
Downstream Solutions
Enerflex refines crude oil, processes petrochemicals, and prepares energy products for marketing and distribution, delivering integrated downstream solutions for industrial applications.
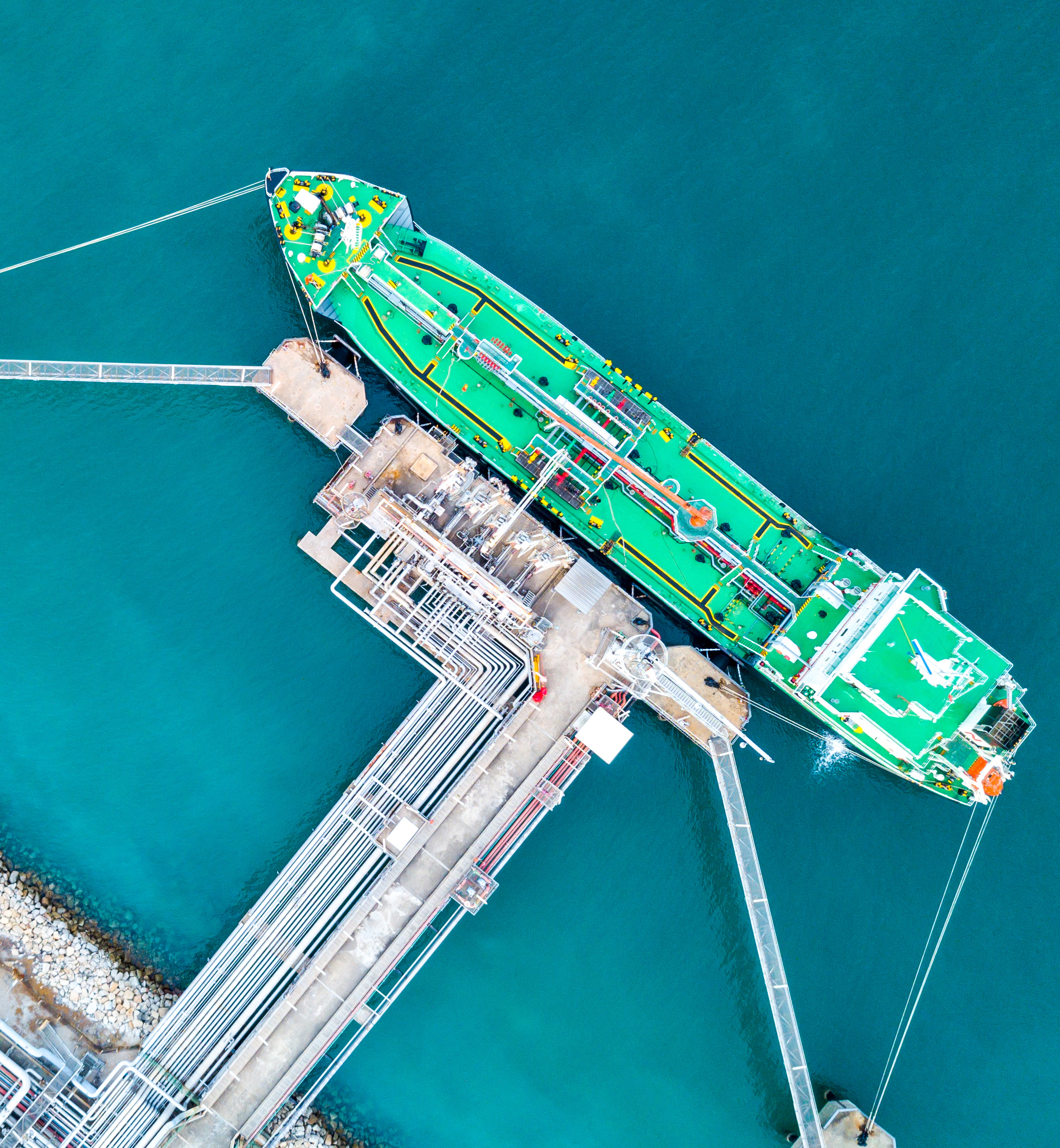
Offshore Packaging
Custom-engineered, skid-mounted, or modularized compression and process solutions for diverse offshore applications, designed to meet multiple specifications across industries.
Case Study
Louisiana, USA – 6,800 TR Propylene Refrigeration System
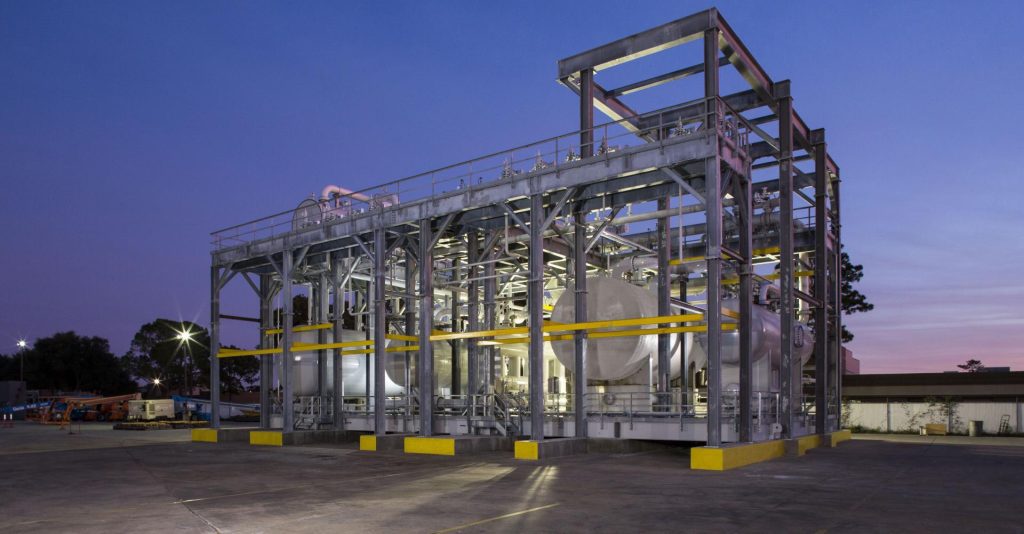
Challenge:
Enerflex was tasked with engineering, designing, and manufacturing a large-scale commercial propylene refrigeration system to provide cooling loads for three sets of users.
Solution:
We delivered a fully assembled unit (without the drivetrain) measuring 86′ L x 56′ W x 44′ H, including a 9,000 TR water-cooled condenser weighing over 105 tons.
Outcome:
The modularized approach successfully reduced costs and maximized installation efficiency, meeting the client partners’ expansion needs on time and within budget.
Case Study
Third Train Gas Processing Facility
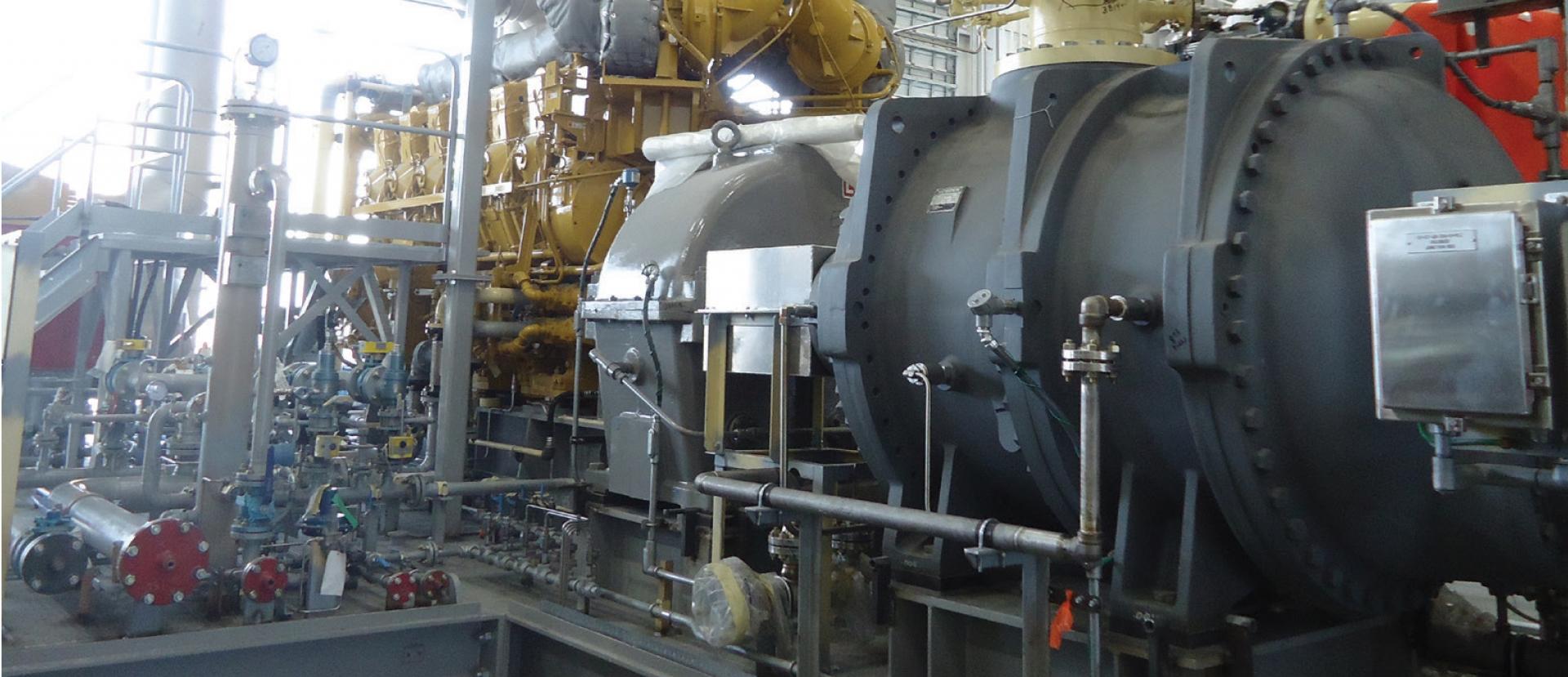
Challenge:
This three-year project, located in Northwest Kazakhstan, involved a unique refrigeration solution for the third train of a gas processing facility as part of the client partner’s plan to double production.
Solution:
Enerflex engineered and supplied three screw compressors, each powered by a 3,700 HP gas engine with a step-up gearbox, spinning the compressor at 2,000 RPM.
Outcome:
Enerflex’s in-country regional team handled the initial design, while the team in Houston completed the detailed design and manufacturing. This collaborative approach between regions optimized our efficiency.
The Enerflex Portfolio
Process Refrigeration
- Refinery / Petrochemical
- LNG Liquefaction
- Hydrocarbon Import / Export Terminals
- Storage Tanks
- Midstream Gas Processing
- Ammonia Fertilizer Plants
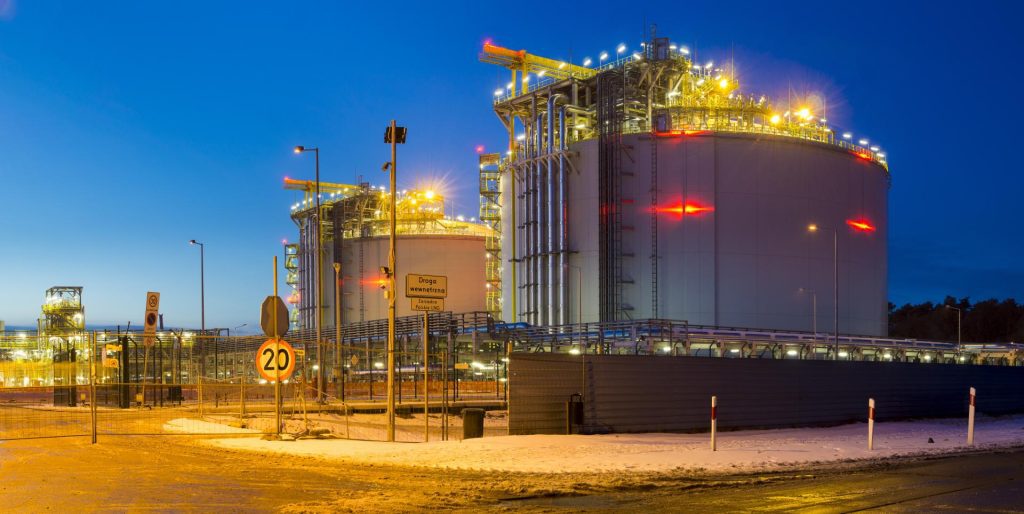
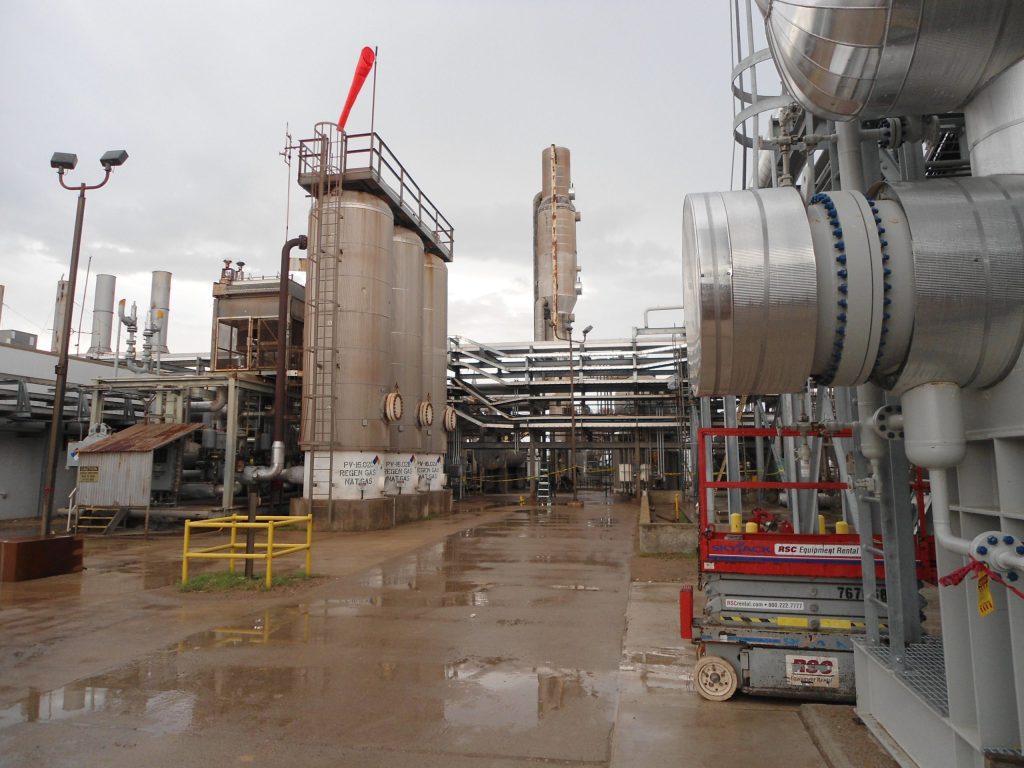
Industrial Refrigeration
- Industrial Gases
- Power Plants
- Pharmaceutical Plants
- Food and Beverage
- Ammonia Absorption Systems
Certifications
Our refrigeration equipment always meets the most stringent API compliance standards.
- ASME
- PED
- CRN
- NR-13
- KGS
- CU-TR (GOST)
- CEC
- IEC/ATEX
- CSA
- AS
- INMETRO
- KOSHA/KTL