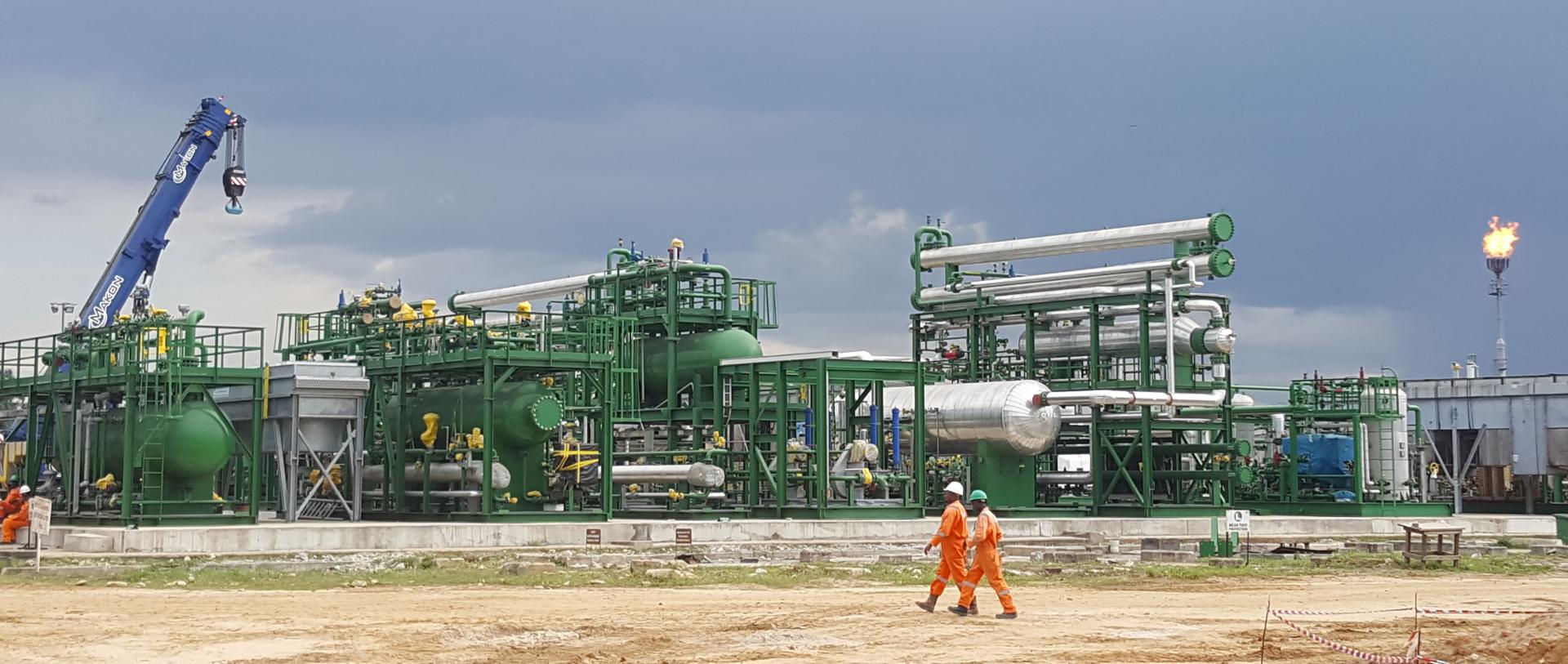
Equipment / Gas Treating
Inlet Separation and Filtration
Custom Solutions for Every Contaminant
We deliver separation and filtration systems designed to handle any combination of solid and liquid contaminants in all flow states. Our solutions keep your operations running smoothly, ensuring efficient, effective hydrocarbon processing.
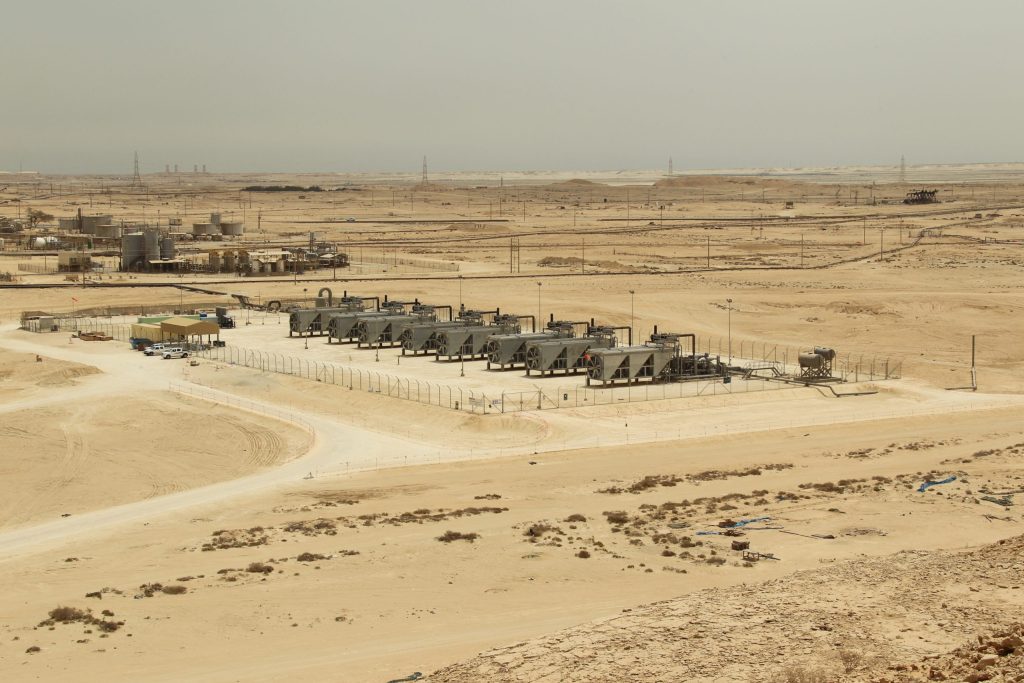
Built for Complex Contamination Challenges
Enerflex’s separation and filtration systems enhance uptime, improve productivity, and cut costs by removing contaminants like iron oxides, sulfides, dirt, and deformable particles. Designed for varying gas and liquid compositions, our solutions ensure reliable performance.
The Enerflex Edge
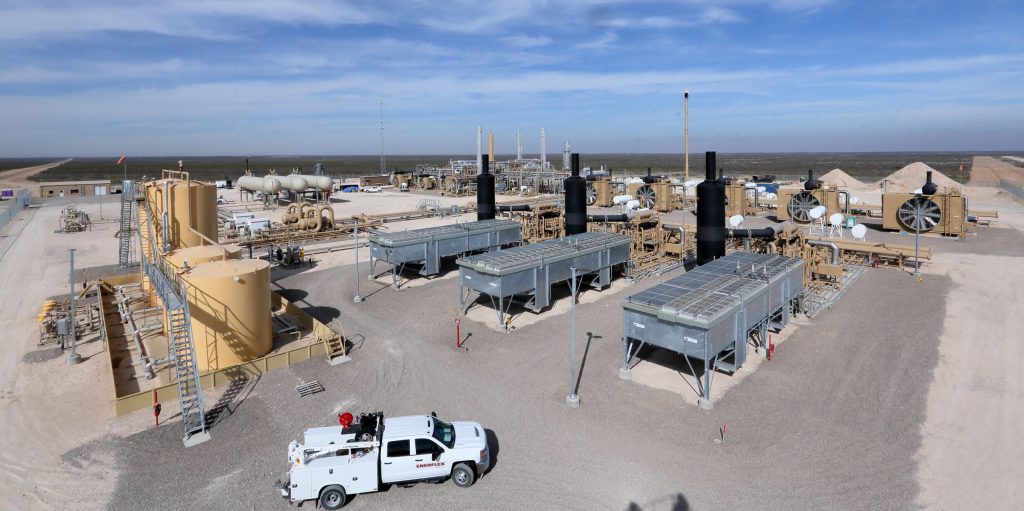
Drawing from Decades of Experience
Our inlet separation designs draw from hundreds of natural gas processing plants we’ve built globally, ensuring reliable solutions designed for diverse operational needs.
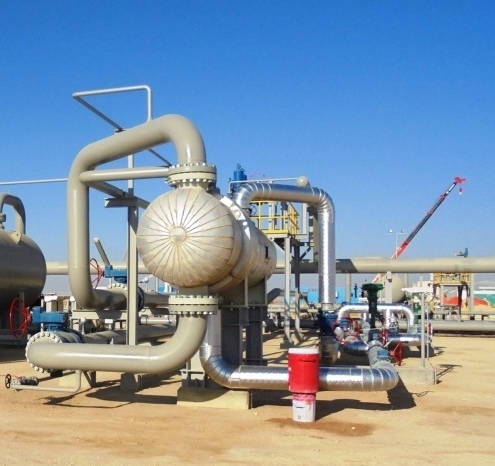
Protecting and Prolonging Equipment Life
Our filtration systems are engineered to remove contaminants effectively, reducing wear on critical equipment and lowering maintenance costs, while minimizing downtime to extend asset longevity.
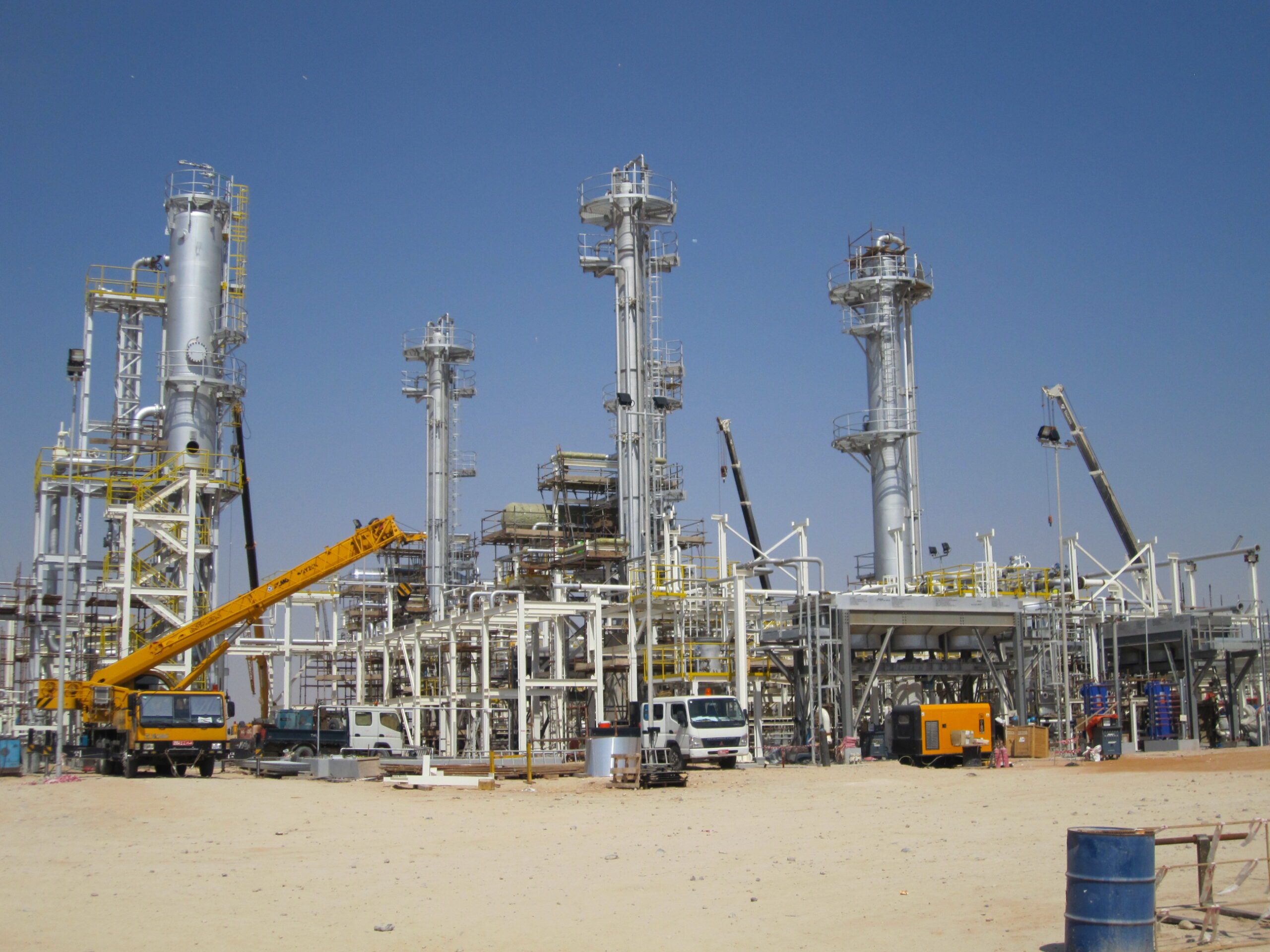
Maximizing Efficiency and Performance
We deliver high-performance filtration solutions that enhance operating efficiency across the gas and liquid hydrocarbon value chain—covering production, processing, transportation and refining.
Solutions
Specialized Inlet Separation and Filtration
- Slug Catcher
- 2-Phase / 3-Phase Separators
- Test and Group Separators
- Desand Separator
- Blowcase
- Inlet Coalescer
- Cyclone Separators
Case Study
200 MMSCFD Two-Phase Sour Gas Processing Facility
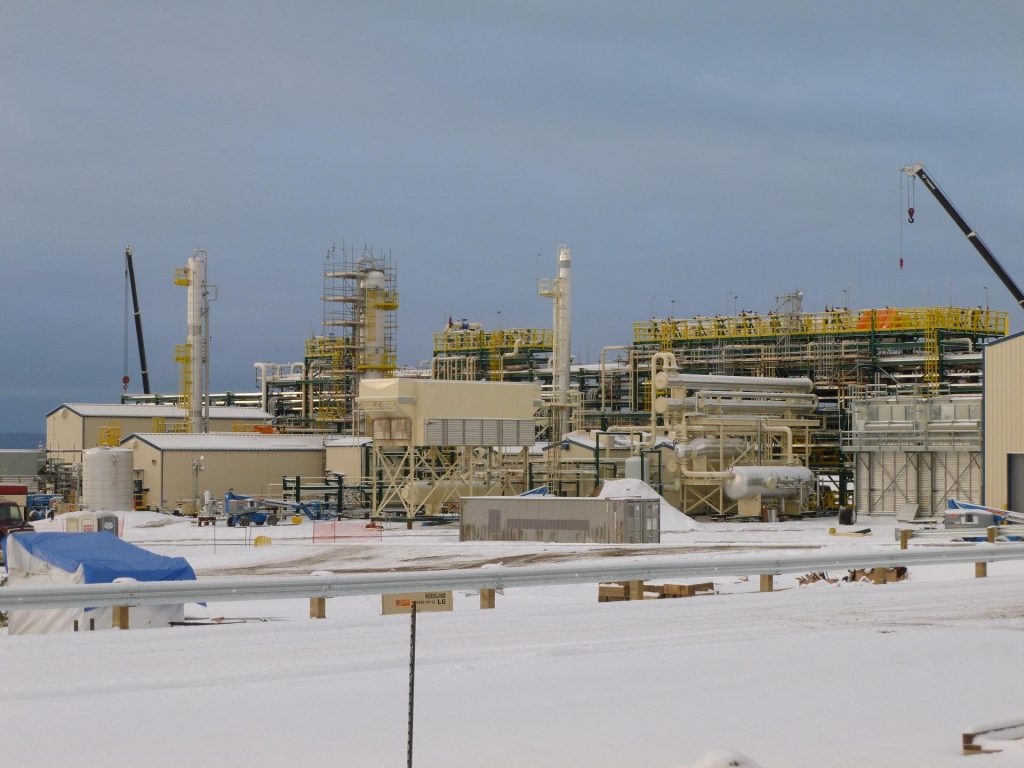
Challenge:
Driven by the expanding Montney gas play, our client partner in British Columbia, Canada, needed a large, two-phase sour gas processing facility to handle raw natural gas. The project required comprehensive processing capabilities to meet rigorous timelines and operational needs.
Solution:
We engineered, designed, and manufactured a double-train gas processing plant in two phases. Phase 1 included a 100 MMSCFD hydrocarbon dew point plant, an amine plant, an inlet separator, a vapour recovery compression package (1,150 HP electric motor drive), an acid gas dehydration package and a condensate stabilizer package. In Phase 2, we delivered an additional 100 MMSCFD amine plant and hydrocarbon dew point plant.
Outcome:
Enerflex completed the project on time, meeting all specifications and ensuring seamless gas processing.
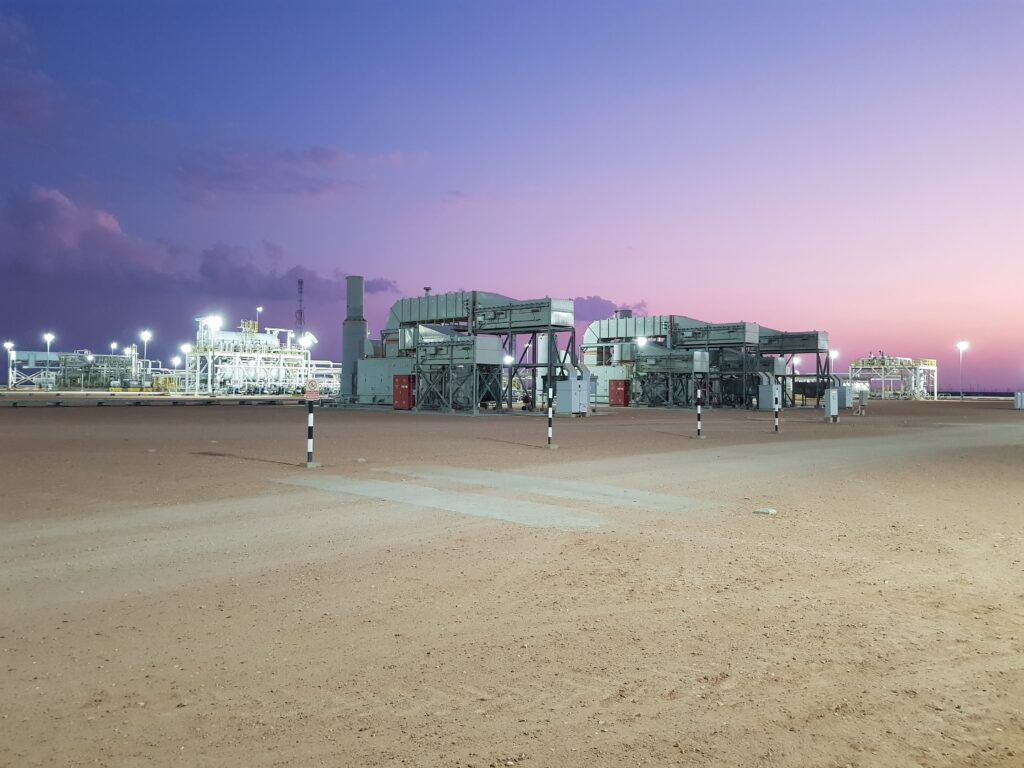
Build-Own-Operate-Maintain Solutions
Our BOOM model covers all aspects of inlet separation and filtration systems—spanning design, construction, operation, and maintenance. This approach ensures effective contaminant removal, cost certainty and faster time-to-market.