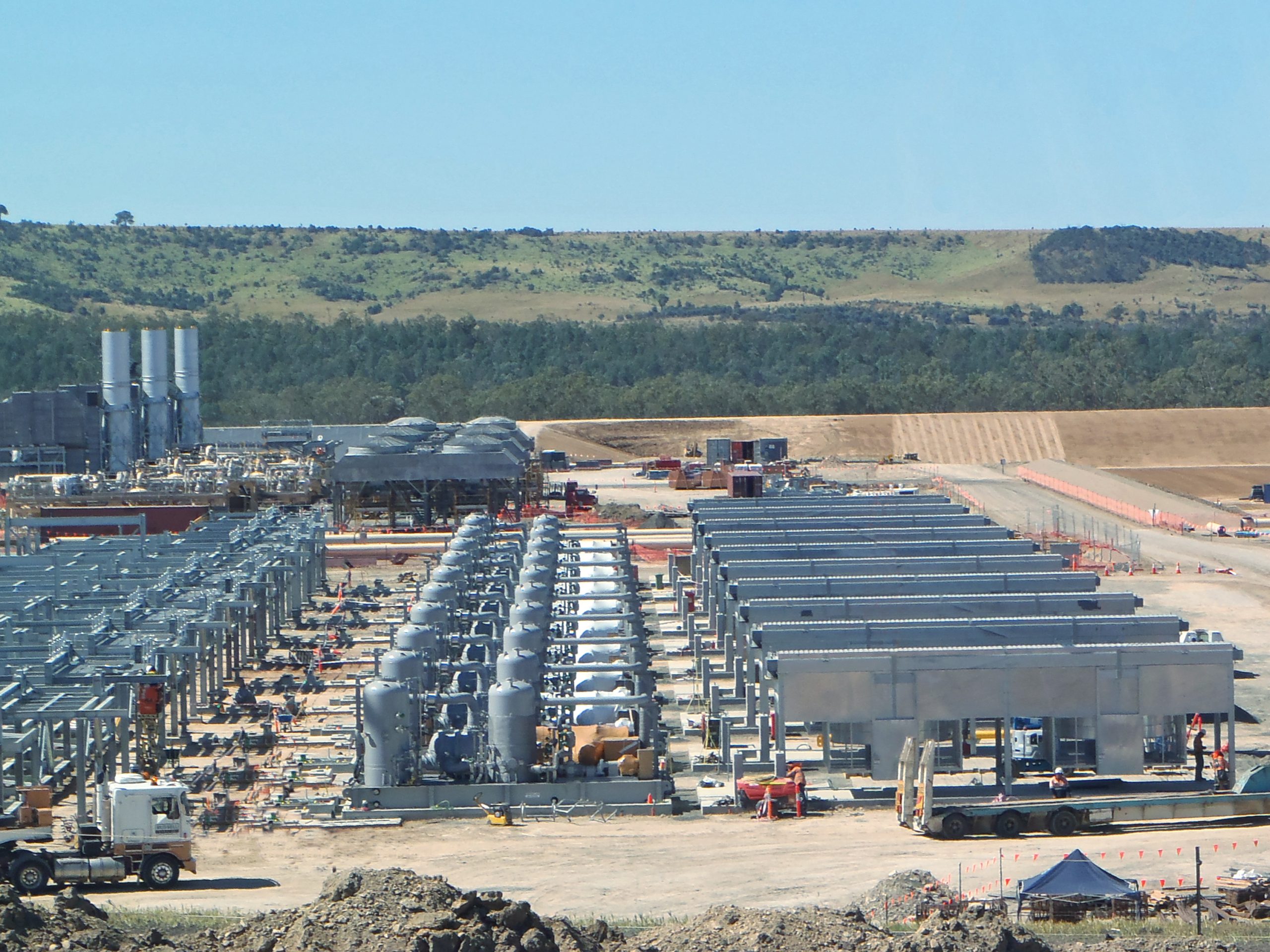
Equipment / Compression
Rotary Screw Compression
Efficient compression for high-volume, lower-pressure applications
Our rotary screw compressors are designed to optimize gas throughput at lower pressures. Built for durability, these compressors perform even in the toughest conditions.
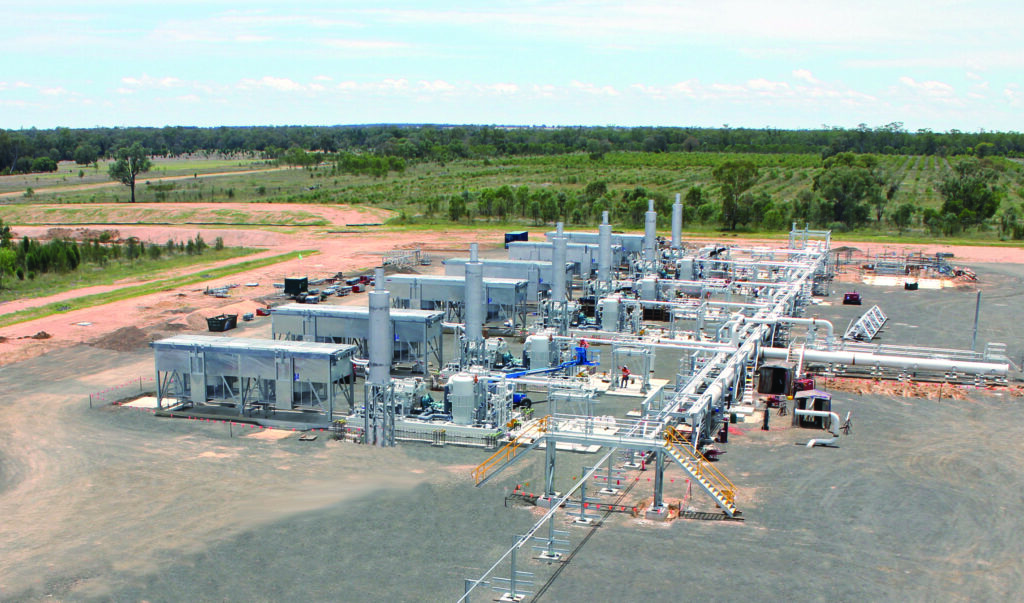
Why Choose Rotary Screw Compression?
Rotary screw compressors are highly efficient, quieter, and require less frequent maintenance than reciprocating models. With larger motors, they handle higher air volumes, making them ideal for continuous-duty applications.
Solutions
Enerflex provides rotary screw compression solutions for:
- Gas Lift
- Booster / Pipeline
- Overhead
- Residue
- Gathering / Wellhead
- Inlet
- Storage
- Reinjection
- VRUs
- Coal Seam Gas (CSG)
- Offshore Floating Production and FPSOs
- Enhanced Oil Recovery (EOR)
The Enerflex Edge
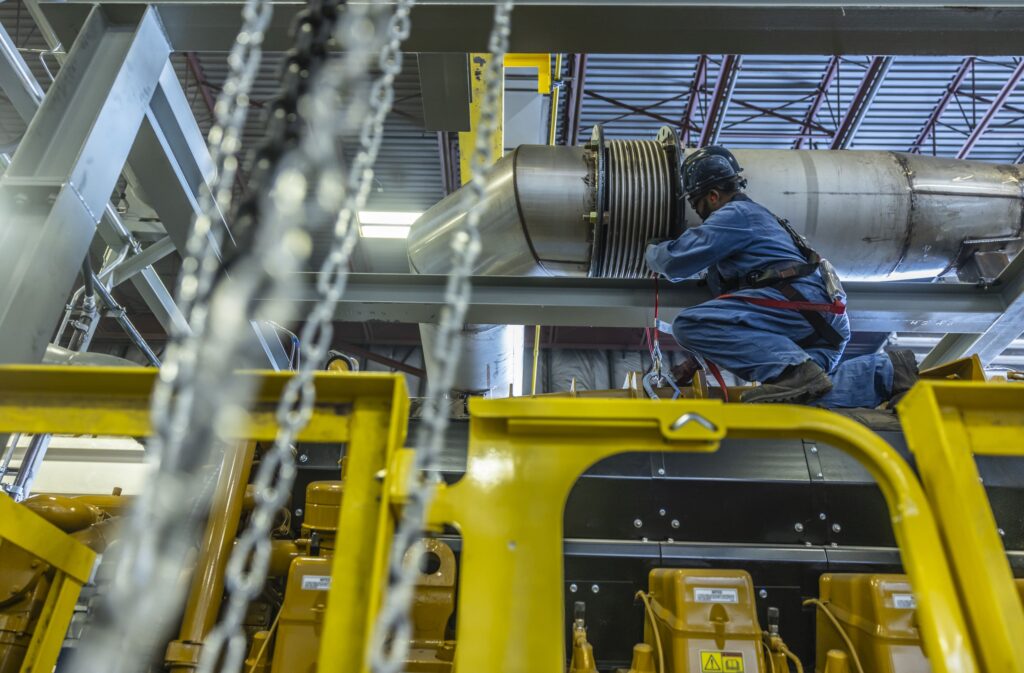
Proven Durability from In-House Manufacturing
Enerflex leverages insights from its extensive number of rotary screw compressor installs to optimize flow-rates even under tough conditions like sour gas service. By using our own manufacturing facilities, we ensure each unit is built to last, tested, and optimized for maximum durability and performance.
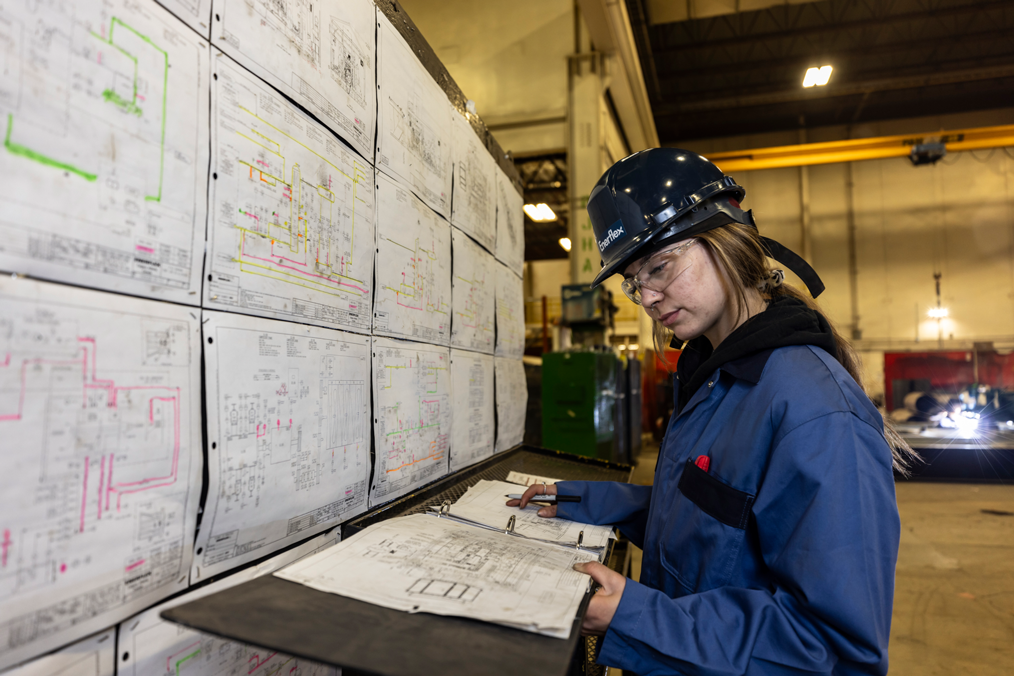
Flexible Solutions for Every Application
We offer rotary screw compressors ranging from 20 HP to 5,000 HP. Whether you need standard plug-and-play options or fully customized designs, our compressors handle high volumes at lower suction and discharge pressures, making them ideal for a wide range of gas applications.
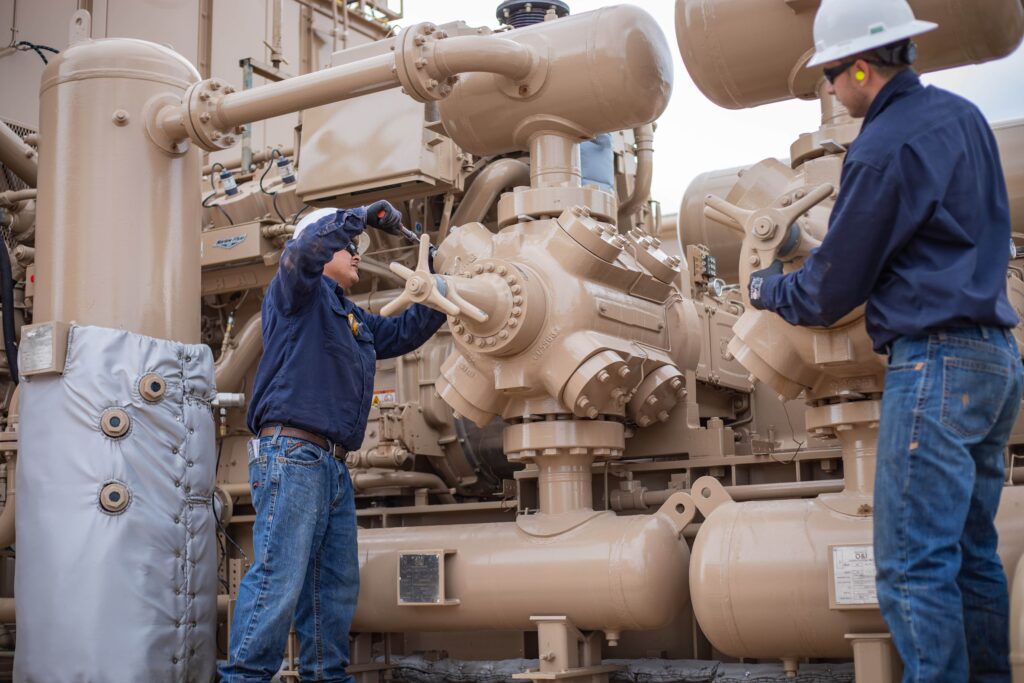
Seamless Service from Build to Operation
Enerflex’s service hub provides an unmatched advantage, with the same company that manufactures the equipment handling installation and maintenance. Our technicians, trained on our own systems, ensure quick issue resolution and streamlined performance, reducing downtime and increasing reliability for our clients.
Case Study
High Horsepower Rotary Screw Compression
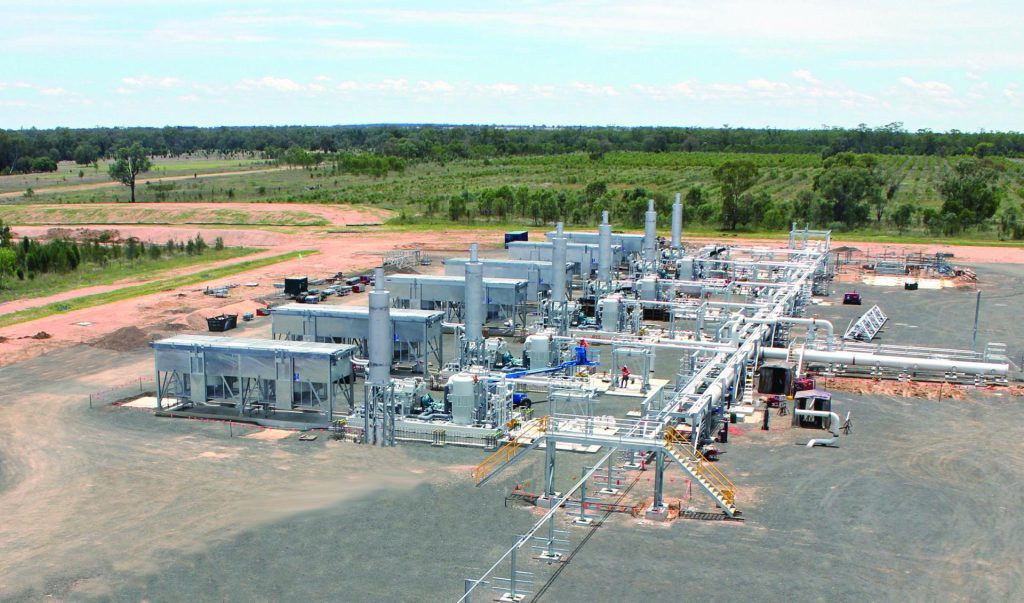
Challenge:
Enerflex was tasked with fabricating and assembling 19 hubs, each containing four rotary screw compressors and inlet separation units. These units needed to gather low-pressure coal seam gas (200 kPag) and compress it to 1,900 kPag. Given the remote location in Queensland, Australia, the hubs were fabricated and assembled in North America before being disassembled and containerized for shipment to Brisbane.
Solution:
The first unit underwent a complete string test in Calgary to verify the design’s function. After optimizing the design on the second unit, the remaining 69 compressor packages were fabricated in the USA.
Outcome:
This project marked a world-first achievement, producing LNG from coal seam gas. The sales gas is transported to Gladstone, converted to LNG, and exported.
Case Study
Rotary Screw Compression Project for Rail Car Unloading
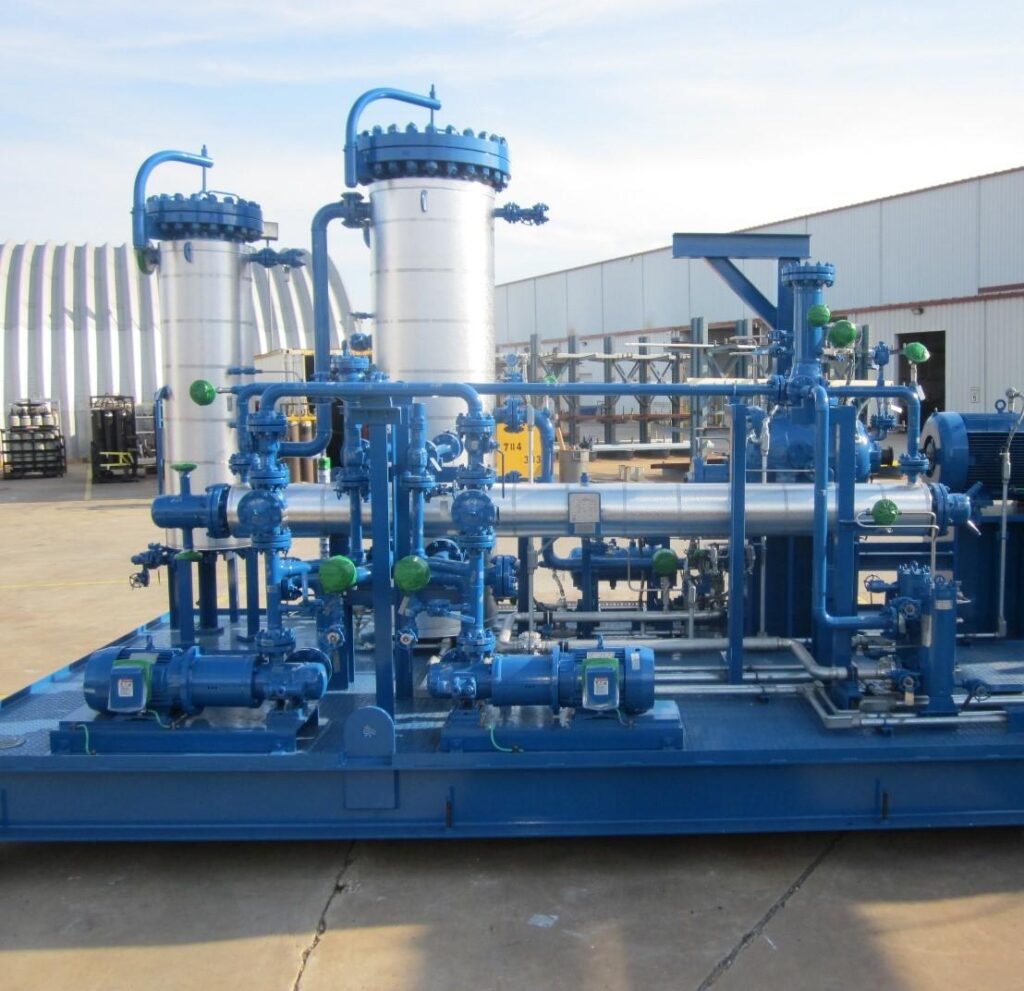
Challenge:
Enerflex was engaged to replace redundant Frick units with two Howden WCV-204 rotary screw compressors, driven by Siemens 200 HP motors. The compressors were needed to unload propylene and propane mixtures from rail cars, requiring precise pressure control for vapour displacement and recovery during cyclical unloading operations.
Solution:
Our system included API 619 compressors and API 614 lube oil systems with dual oil pumps, a single shell and tube oil cooler, and advanced suction scrubbers. Critical integration between the Siemens PLC program and the existing systems ensured smooth operation.
Outcome:
The project, located in Pasadena, Texas, was successfully completed through close collaboration between Enerflex and the operator. Software simulations were performed to minimize commissioning delays, ensuring the system was up and running efficiently.